Manual Differential Drive, 18 mm Travel
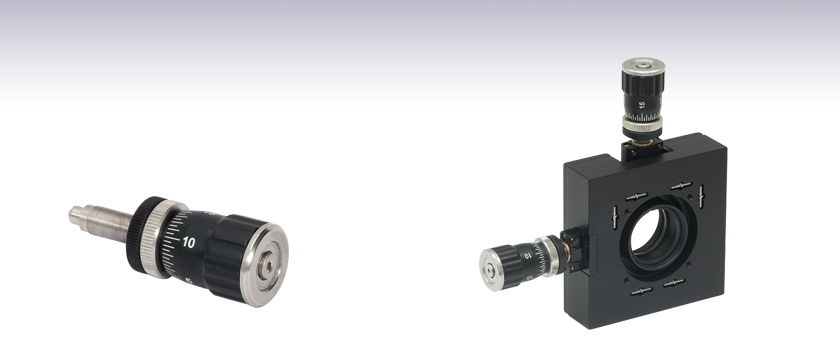
- Lockable Coarse Adjustment:
Range: 0.72" (18.3 mm)
Pitch: 0.012" (300 µm) per Revolution - Fine Adjustment:
Range: 0.01" (250 µm)
Pitch: 0.001" (25 µm) per Revolution
Application Idea
Our ST1XY-D Translation Stage
Incorporates a DM22 Micrometer
DM22

Please Wait
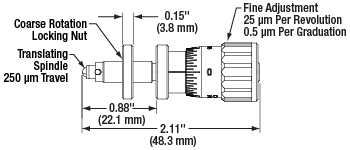
Features
- Fine Adjustment Range: 250 µm
- Fine Adjustment per Revolution: 25 µm
- Coarse Adjustment Range: 0.72" Long 1/4"-80 Threads
- Coarse Adjustment per Revolution: 0.012" (80 TPI)
- On-Axis Load Capacity: 11 lbs (5 kg)
The DM22 Differential Adjuster uses two internal leadscrews; one pushes the center spindle forward at 400 µm per revolution while the other pulls it back at 375 µm per revolution. The resultant total forward motion of the center spindle is just 25 µm for one complete revolution of the graduated knob. Each small graduation of the fine control knob is 0.5 µm; the smallest incremental move for the DM22 is approximately 50 nm. When performing fine adjustment the coarse adjustment mechanism can be locked by means of a small locking collar. For more details on the operating mechanism of the DM22, please refer to the DM22 Operation tab.
Prior to installation, the adjuster should be greased slightly. To install the adjuster, screw the threads into the bushing by hand. Ensure that cross threading does not occur in order to avoid damage to the adjuster and bushing.
If the fine adjustment knob on the DM22 is ever removed from the actuator body, it can be reattached. Please see the DM22 Knob Attachment tab for more details. Follow the reattachment instructions carefully so that the actuator functions properly.
Fine Adjustment Knob Reattachment for Differential Adjusters
- Step 1: Fully remove the detached knob.
- Step 2: Apply pressure to the tip of the actuator.
- Step 3: While maintaining pressure, screw in the knob 2 to 3 threads.
- Step 4: Once threaded, remove pressure from Step 2 and continue to slowly screw in the knob. Please note that this should be done slowly and with little force. If too much force is applied, cross-threading may occur and may damage the threads.
Differential Adjuster Operation Mechanisms
A differential adjuster consists of four basic parts: outer body, coarse adjustment lock, inner spindle, and fine adjustment knob. Using the DM22 as an example, the video to the left demonstrates how these four parts come together to create a device that allows for coarse and fine adjustments. Also detailed are two different methods of mounting these actuators into an assembly.
Differential Adjuster Mechanisms
- Outer Body:
- Provides Coarse Adjustment
- Contains Internal Threads with a Pitch Smaller than the External Threads of the Inner Spindle
- Coarse Adjustment Lock:
- Prevents the Outer Body from Rotating; Locks Coarse Translation
- Enables Fine Adjustment
- Inner Spindle:
- Mounted within Outer Body
- Contacts the Moving Platform and will Translate with the Coarse Adjuster
- Contains External Threads with Greater Pitch than the Internal Threads of the Outer Body
- Fine Adjustment Knob:
- Internal and External Threads that Match the Inner Spindle and the Outer Body Threads
- Rotating the Knob Provides Inner Spindle Translation that is Equal to the Difference Between the Two Thread Pitches
Posted Comments: | |
user
 (posted 2021-05-05 05:56:27.667) Hi!
1. Shouldn't the DDM2 be able to withstand higher loads considering that each of the two interna threads probably can withstand 5-10x the stated maximum load without damage?
2. I suppose that the fine adjustment is self locking due to it's fine pitch but is there some way of adding security to this for installations that need very long term stability and may have some slight vibrations? cdolbashian
 (posted 2021-09-10 10:51:51.0) Thank you for reaching out to us Magnus!
1. You are indeed correct that the screw threads would be able to support more load than we spec. We spec this as a max load to maintain the fine adjustment sensitivity and a smooth motion over the full range of travel.
2. The locking mechanism which would be implemented would actually interfere with the micron-accuracy positioning, so in this case it was not included, as the act of locking would disturb a finely achieved position. Michael Van de Graaff
 (posted 2019-09-25 20:05:12.07) You should probably put a link to this product DM22 on other pages, like for example: https://www.thorlabs.com/newgrouppage9.cfm?objectgroup_id=1811
I spent a while looking for this exact product (which i didn't know for sure even existed, i only assumed) before I gave up and bought something that would get the job done from one of your competitors.
then I found this exact product in the bottom of my micrometer drawer and realized it would fit into my platform mount. so yeah, this product is a perfect quick solution for anywhere a 1/4"-80 normal adjustment screw isn't good enough YLohia
 (posted 2019-09-27 12:40:32.0) Hello, thank you for your feedback. We looked into the search keywords for the DM22 and found that to be lacking, so we have updated our search engine directory and will look into cross-linking these in the future. Alexander.Zolot
 (posted 2017-11-07 18:06:01.457) Regarding DM22: Is there a version of this product that is compatible with the 1/4"-100 threads in the Polaris-series mounts? (Is this item compatible with that in some way that is unclear from website details?) nbayconich
 (posted 2017-11-15 08:19:22.0) Thank you for contacting Thorlabs. We have not yet designed a 1/4"-100 threaded version of this differential adjuster but we can look into providing a custom version for our POLARIS series mounts. I will reach out to you directly with more information about our custom capabilities. djarami
 (posted 2015-03-06 13:17:04.577) I need a little more information on the DM22 part or ones similar to it. I would like to see a video on how to install it, use it, etc. I really do like all the different CAD models available for your parts! It helps to design the other parts it will work with. cdaly
 (posted 2015-03-11 12:17:32.0) Response from Chris at Thorlabs: The differential micrometer DM22 must be mounted to some other item by its outer 1/4"-80 threading. This threading provides the course adjustment of the micrometer, which is moved by turning the knurled surface just inside of the rear knob. The course adjustment is locked by threading down the locking nut/collar against the item to which the DM22 is mounted. Inside this now fixed, 1/4"-80 threaded main body, which I will call the outer spindle, is an inner spindle which is able to slide axially within, but is unable to rotate. Both the inner spindle and outer spindle are threaded to the rear knob via two different threads with different pitches. When the knob is rotated, It will translate relative to the fixed outer spindle, via a 400 um/rev thread, while the inner spindle translate relative to the knob via a 375 um/rev thread, resulting in a translation of the inner spindle relative to the fixed outer spindle of 25 um/rev. isaac.theurkauff
 (posted 2014-02-24 17:05:14.91) Hello.
After unscrewing beyond the limit, the screw is now blocked, and I am unable to scre it back. What should I do?
Thanks. jlow
 (posted 2014-02-28 11:19:50.0) Response from Jeremy at Thorlabs: You have to screw this back on very carefully. Do not force it in because that can destroy the threads. I will contact you directly on putting this back on. tcohen
 (posted 2012-05-24 15:28:00.0) Response from Tim at Thorlabs: The rated axial (push) torque for the DM22 is < 11ft-lbs (15Nm) before the threads corrupt. tesar
 (posted 2012-05-24 10:27:17.0) What is the on-axis load capacity of the DM22 Differential Adjuster? jjurado
 (posted 2011-08-29 13:49:00.0) Response from Javier at Thorlabs to jdthomps: Thank you very much for your feedback. As a differential adjuster, the DM22 was not designed to include markings on the fine adjustment knob for absolute position measurement. I will contact you directly to help you find an alternative solution. jdthomps
 (posted 2011-08-22 17:37:32.0) This actuator would be much more useful with a graduated scale on the fine adjustment, which would allow you to know the absolute position instead of the position modulo 1 turn. |