Supermirrors
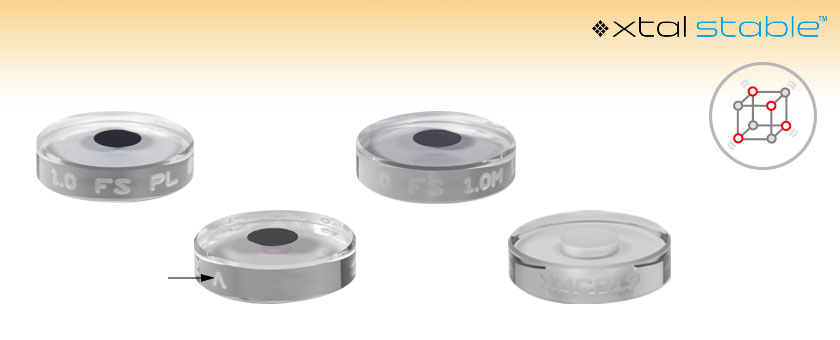
- Single-Crystal GaAs/AlGaAs Coating
- Ø8 mm Coating on Ø1", 6.35 mm Thick Fused Silica
- Wavelength Options: 1064 nm, 1156 nm, 1397 nm, 1550 nm
- Options With Up to 300 000 Finesse
XM15P8
Plano Crystalline Supermirror,
Thermo-Optic Noise Optimized,
1064 nm
XM16R8
Concave Crystalline Supermirror,
1 m Radius of Curvature, 1156 nm
Engraved Caret Indicates Side with Crystalline Coating
Lower Brownian Noise*
*When Compared to Sputtered Amorphous Thin-Film Coatings
XMCR19
Ø1" Compensation Ring with Ø9 mm Through Hole

Please Wait
Features
- Ø8 mm Single-Crystal GaAs/AlGaAs Optical Coating
- Extremely High Reflectance at Center Wavelength
- R > 99.9969% or R > 99.9984% for 1064 nm
- R > 99.999% for 1156 nm
- R > 99.999% for 1397 nm
- R > 99.9984% or R > 99.999% for 1550 nm
- Ø5 mm AR Coating on Back
- Ø1", 6.35 mm Thick Fused Silica Substrate
- Ready for Optical Contacting to Spacers or Compensation Rings
- Low Optical Absorption and Scatter
- Low Thermal Resistivity
- Plano and Concave (1 m Radius of Curvature) Options
- Thermo-Optic Noise Optimized Coating Available for 1064 nm
- Individual Data Sheets for Each Supermirror
- Ø1" Compensation Rings Sold Below
Applications
- High-Finesse Laser Cavities
- Low-Noise Precision Interferometry
- High-Power Laser Systems
- Ultrastable Lasers for Atomic Clocks
- Mirrors for Gravitational Wave Detection
Thorlabs offers high-performance, single-crystal supermirror coatings on Ø1" substrates for applications requiring the highest reflectance possible at a specific wavelength. Plano and concave options with Ø8 mm coatings at 1064 nm, 1156 nm, 1397 nm, or 1550 nm are available from stock below. The front face coatings are fabricated using a patented molecular beam epitaxy process (U.S. Patent: 9,945,996; E.U. Patent 3219832A1) that enables monocrystalline semiconductor materials like GaAs/AlGaAs to exhibit quasi-bulk properties and lower elastic loss than amorphous, dielectric coatings created from sputtering. See our crystalline mirror coatings page for details. The back side of each crystalline mirror is AR coated for the same center wavelength as the crystalline coating on the front face. Both faces of the optic are super-polished so that they can be optically contacted to cavity spacers or compensation rings. Ø1" compensation rings for stabilizing the zero-crossing temperature of the coefficient of thermal expansion in cavities that use these mirrors are sold below.
These high-performance supermirrors with ultralow optical absorption and minimal Brownian noise are key ingredients for the construction of optical atomic clocks, compact optical reference cavities, and stabilized lasers, as well as the next generation of gravitational wave detectors. The high-quality-factor single-crystal coatings used in our xtal stable™ optics substantially reduce inherent thermomechanical fluctuations, enabling a significant improvement in the overall frequency stability of precision interferometers. Thorlabs also offers two mirrors for use at 1064 nm with coatings designed to minimize thermo-optic noise. Our crystalline coatings have been employed in groundbreaking experiments and cutting edge commercial systems pushing the limits of laser linewidth and cavity noise performance.
Each of our crystalline supermirrors is individually tested using a cavity ring-down setup to ensure the extremely high reflectance and low transmission at the center wavelength. Click here to view a sample data sheet. More details on the design of these supermirrors and our robust measurement process can be found in the Measurement tab.
We offer optical contacting services for the construction of custom optical cavities using stock mirrors listed below. If unique coatings are required for your application, we provide a variety of high-performance, single-crystal supermirror coatings and novel manufacturing processes for large-volume OEM customers. For more information on our custom mirrors and cavities, see our crystalline mirror coatings capabilities page or contact Tech Support.
Supermirror Specifications | |||||||||||||
---|---|---|---|---|---|---|---|---|---|---|---|---|---|
Item #s | XM11P8 | XM11R8 | XM15P8 | XM15R8 | XM16P8 | XM16R8 | XM23P8 | XM23R8 | XM12P8 | XM12R8 | XM14P8 | XM14R8 | |
Center Wavelength | 1064 nm | 1156 nm | 1397 nm | 1550 nm | |||||||||
Mirror Shape | Plano | Concave | Plano | Concave | Plano | Concave | Plano | Concave | Plano | Concave | Plano | Concave | |
Finessea | 100 000 | 200 000 | 300 000 | 300 000 | 200 000 | 300 000 | |||||||
Crystalline Coating Reflectanceb | >99.9969% at 1064 nm |
>99.9984% at 1064 nm |
>99.999% at 1156 nm |
>99.999% at 1397 nm |
>99.9984% at 1550 nm |
>99.999% at 1550 nm |
|||||||
Crystalline Coating Transmissionb | >5 ppm at 1064 nm | >3.5 ppm at 1064 nm | >3.5 ppm at 1156 nm | >3.5 ppm at 1397 nm | >5 ppm at 1550 nm | >5 ppm at 1550 nm | |||||||
Crystalline Coating Loss Angleb,c | <4 x 10-5 at 300 K <5 x 10-6 at 10 K |
||||||||||||
Damage Thresholdd | CWe | 46.2 kW/cm (1064 nm, Ø5.5 mm) | |||||||||||
Pulsed | 5 J/cm2 (1030 nm, 10 ns, 10 Hz, Ø0.240 mm) | ||||||||||||
AR Coating Reflectance (Back Sidef) | <0.1% at Center Wavelength; 0° AOI over Central Ø5 mm | ||||||||||||
Substrate Material | Corning 7980 0A UV Fused Silicag | Corning 7980 0A UV Fused Silicagg |
Corning 7979 0A IR Fused Silicag |
Corning 7980 0A UV Fused Silicag | |||||||||
Surface Roughness | Crystalline Coating: <1.5 Å (RMS) Back Sideh: <1.5 Å (RMS) |
Crystalline Coating: <1.5 Å (RMS) Back Sideh: <1 Å (RMS) |
Crystalline Coating: <1.5 Å (RMS) Back Sideh: <1 Å (RMS) |
Crystalline Coating: <1.5 Å (RMS) Back Sideh: <1 Å (RMS) |
Crystalline Coating: <1.5 Å (RMS) Back Sideh: <1.5 Å (RMS) |
Crystalline Coating: <1.5 Å (RMS) Back Sideh: <1 Å (RMS) |
Plano Mirror Specifications | ||
---|---|---|
Side of Optic | Front Sidea | Back Sideb |
Surface Flatness (Peak to Valley) |
<λ/10 at 633 nm over Central Ø10 mm | <λ/10 at 633 nm over Central Ø19.5 mm |
Surface Quality | 10-5 Scratch-Dig over Central Ø10 mm, 20-10 Scratch-Dig from Ø10 mm to Bevel |
20-10 Scratch-Dig over Central Ø19.5 mm |
Concave Mirror Specifications | ||
---|---|---|
Side of Optic | Front Sidea | Back Sideb |
Radius of Curvature | 1 m (Central Ø18.5 mm) Plano (Annular Region between Ø18.5 mm and Bevel) |
Plano over Central Ø19.5 mm |
Surface Flatness (Peak to Valley) |
<λ/10 at 633 nm in Annular Region between Ø18.5 mm and Bevel |
<λ/10 at 633 nm over Central Ø19.5 mm |
Surface Irregularity (Peak to Valley) |
<λ/10 at 633 nm over Crystalline Coating (Ø8 mm) | N/A |
Surface Quality | 10-5 Scratch-Dig over Central Ø10 mm, 20-10 Scratch-Dig in Annular Region Between Ø18.5 mm and Bevel |
20-10 Scratch-Dig over Central Ø19.5 mm |
Compensation Ring Specifications | ||
---|---|---|
Item # | XMCR19 | |
Material | Premium Grade ULE®* | |
Clear Aperturea | Chamfer to Through Hole | |
Side of Optic | Front Sidea | Back Side |
Surface Flatness | <λ/4 at 633 nm | Commercial Polish |
Surface Quality | 20-10 Scratch Dig | Commercial Polish |
*ULE is a registered trademark of Corning, Inc.
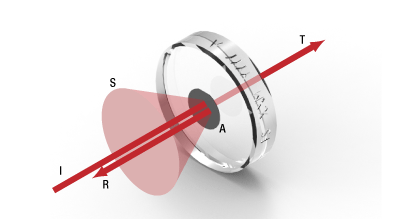
Figure 1: Components of Optical Power Through Crystalline Supermirror; I = Incident Optical Power, S = Scattering, A = Absorption, R = Reflection, T= Transmission.
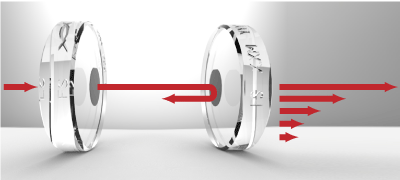
Figure 2: Light incident on a crystalline supermirror cavity experiences exponential decay for every round-trip through the cavity.
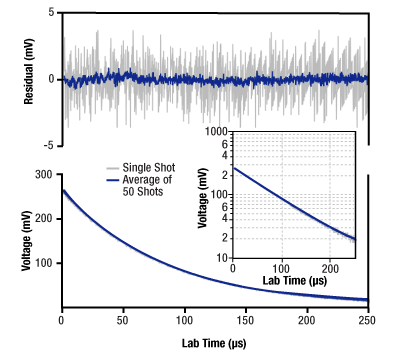
Figure 4: The cavity ring-down setup is used to precisely measure the characteristic exponential decay of the signal. [2]
Cavity Ring-Down
Our crystalline coatings are designed to reflect R > 99.9969% of the incident optical power I, with minimal excess losses from scattering S and absorption A (see Figure 1). Precise and accurate determination of these quantities presents a difficult measurement challenge due to the small values and dynamic range involved. For example, commercial spectrophotometry systems are relatively widely accessible, but will typically provide accuracies at a 0.3% (3000 ppm) level up to reflectivities of approximately 99.9%. Similarly, ratiometric laser power measurements providing 0.01% (100 ppm) accuracies for reflectivities up to 99.99% fall short for characterization needs of these supermirrors. Technical challenges include source amplitude stability, detector linearity over large ranges of optical inputs, and detection noise.
In 1984, Anderson et. al. [1] described a reflectometer based on a resonant optical cavity comprising high-reflectivity end mirrors in order to convert an amplitude measurement into a pure time-delay measurement by exploiting the finite speed of light. When a pulse of light incident reaches the output mirror, a fraction equal to the transmission T is outcoupled and a fraction R is reflected back into the cavity (see Figure 2). On the second round-trip, the same fraction T of this now-reduced incident power is again out-coupled. This ratiometric progression of loss per round trip of the cavity leads to an exponential decay of the transmitted optical power with time constant τ. Critically, this technique is impervious to source amplitude fluctuations, and less sensitive to detector linearity, detection noise, and dynamic range limitations compared to other measurement techniques.
With a measured value of τ and the known cavity length L, the total optical loss (T + S + A) of each supermirror is given by:
T + S + A = L / (cτ)
where c is the speed of light. The optical cavity finesse is also commonly used to describe the optical loss of a cavity. Further decomposition of the losses into the component transmission, scatter, and absorption values is realized as follows: The transmission is a design parameter that can be determined to ~1 ppm precision in our crystalline coatings with knowledge of the indices of refraction of the substrate and coating materials, coupled with measurements of the as-grown layer thicknesses via X-ray diffraction and optionally scanning electron microscopy. Absorption can be directly and independently measured using photothermal common-path interferometry. That leaves scatter as the remaining unknown that can simply be extracted arithmetically.
Measurement Protocol
The total optical loss of each supermirror is measured using a custom-built cavity ring-down system [2]. Figure 3 shows a simplified operational diagram of this setup. Diode lasers are directly coupled—without optical isolation—into a linear cavity formed from a pair of crystalline supermirrors. This arrangement greatly simplifies the system by removing the need for active laser stabilization. The retroreflection of the cavity input coupler forms an extended cavity diode laser and narrows the laser linewidth (as shown in the inset graph in Figure 3). The narrowed linewidth increases the in-coupled optical power by pulling the laser close to the center wavelength of the coating, where the composite laser and external cavity typically has the lowest loss. Irises are used to ensure that the sampled points fall within a radius of 1.5 mm of the center of the mirror substrate. An InGaAs camera is used to align the supermirrors and excite the fundamental TEM00 mode. A fast InGaAs photodiode detects the transmitted optical power. A digital delay generator [3] modulates the laser diode current to zero when the transmitted power exceeds a threshold voltage and triggers data acquisition of a single ring-down transient.
Typical ring-down signals and the residuals generated from a least squares fit to the model
y = ae^(-t / τ) + b
are shown in Figure 4. Additionally, the average of 50 consecutive ring-downs and their fit residuals are displayed, and there are no signs of non-exponential behavior at our highest levels of signal-to-noise ratio.
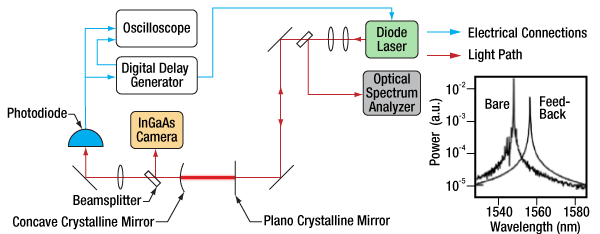
Figure 3: Custom-Built Cavity Ring-Down System for Testing Crystalline Supermirrors [2]; The bare signal is the bare laser spectrum measured by the OSA when the cavity is blocked, while the feedback signal is the measurement of the laser exposed to retroreflection from the cavity.
References
[1] Anderson DZ, Frisch JC, and Masser CS. "Mirror reflectometer based on optical cavity decay time." Applied Optics. April 15, 1984; 23: 1238-1245.
[2] Truong GW, Winkler G, Zederbauer T, Bachmann D, Heu P, Follman D, White ME, Heckl OH, and Cole GD. "Near-infrared scanning cavity ringdown for optical loss characterization of supermirrors." Optics Express. June 24, 2019; 27: 19141-19149.
[3] https://github.com/geedubs/teensytrigger
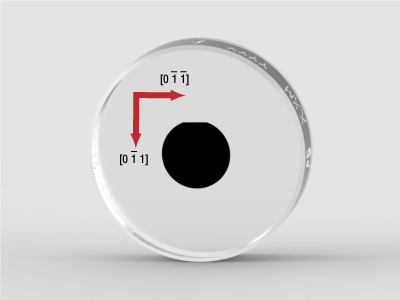
Click to Enlarge
Axes of Single-Crystal GaAs/AlGaAs Coating, with Respect to Coating Flat
Birefringence
As a result of their single-crystal nature, our crystalline coatings exhibit birefringence. It is important to be aware of the birefringence when polarization control is necessary. As can be seen in the figure to the right, the coating disc is marked with a flat along the [0 -1 -1] direction. This flat is parallel to the slow axis of the GaAs/AlGaAs coating. The perpendicular direction, along the [0 -1 1] direction, is the fast axis of the coating.
When incorporating our crystalline supermirrors into a resonant cavity, we recommend that the coating flats are aligned to achieve maximum splitting of the polarization eigenmodes. ("Eyeball" alignment should be sufficient.) The input illumination to the cavity should be linearly polarized either parallel or perpendicular to the flats.
Although research is ongoing, we note that minimum optical absorption by the coating may be observed when the polarization is aligned with the fast axis. More details on this phenomenon can be found in the following manuscript: https://arxiv.org/abs/2009.04721. In addition, it is possible to "tune" the magnitude of the polarization splitting by rotating the end supermirrors with respect to one another.
As a rough estimate, in a linear cavity configuration with the flats aligned, the cavity birefringence, theta, is approximately 1 × 10-3 at both 1064 nm and 1550 nm. A 10 cm long cavity with an input wavelength of 1550 nm would exhibit roughly 500 kHz of polarization splitting.
Damage Threshold Specifications | ||
---|---|---|
Coating Name | Laser Type | Damage Thresholda |
xtal stable™ | CWb | 46.2 kW/cm (1064 nm, Ø5.5 mm) |
Pulsed | 5 J/cm2 (1030 nm, 10 ns, 10 Hz, Ø0.240 mm) |
Damage Threshold Data for our Crystalline Supermirrors
The specifications to the right apply to Thorlabs' crystalline supermirrors sold below. These values are typical and may vary, as each supermirror is made to order.
Laser Induced Damage Threshold Tutorial
The following is a general overview of how laser induced damage thresholds are measured and how the values may be utilized in determining the appropriateness of an optic for a given application. When choosing optics, it is important to understand the Laser Induced Damage Threshold (LIDT) of the optics being used. The LIDT for an optic greatly depends on the type of laser you are using. Continuous wave (CW) lasers typically cause damage from thermal effects (absorption either in the coating or in the substrate). Pulsed lasers, on the other hand, often strip electrons from the lattice structure of an optic before causing thermal damage. Note that the guideline presented here assumes room temperature operation and optics in new condition (i.e., within scratch-dig spec, surface free of contamination, etc.). Because dust or other particles on the surface of an optic can cause damage at lower thresholds, we recommend keeping surfaces clean and free of debris. For more information on cleaning optics, please see our Optics Cleaning tutorial.
Testing Method
Thorlabs' LIDT testing is done in compliance with ISO/DIS 11254 and ISO 21254 specifications.
First, a low-power/energy beam is directed to the optic under test. The optic is exposed in 10 locations to this laser beam for 30 seconds (CW) or for a number of pulses (pulse repetition frequency specified). After exposure, the optic is examined by a microscope (~100X magnification) for any visible damage. The number of locations that are damaged at a particular power/energy level is recorded. Next, the power/energy is either increased or decreased and the optic is exposed at 10 new locations. This process is repeated until damage is observed. The damage threshold is then assigned to be the highest power/energy that the optic can withstand without causing damage. A histogram such as that below represents the testing of one BB1-E02 mirror.
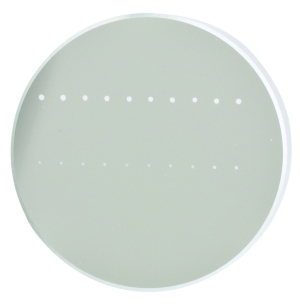
The photograph above is a protected aluminum-coated mirror after LIDT testing. In this particular test, it handled 0.43 J/cm2 (1064 nm, 10 ns pulse, 10 Hz, Ø1.000 mm) before damage.
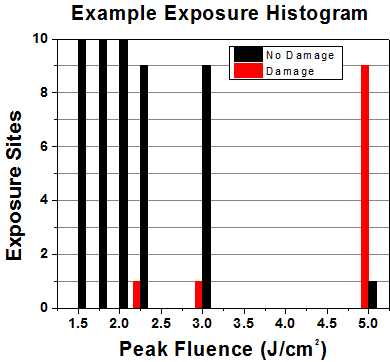
Example Test Data | |||
---|---|---|---|
Fluence | # of Tested Locations | Locations with Damage | Locations Without Damage |
1.50 J/cm2 | 10 | 0 | 10 |
1.75 J/cm2 | 10 | 0 | 10 |
2.00 J/cm2 | 10 | 0 | 10 |
2.25 J/cm2 | 10 | 1 | 9 |
3.00 J/cm2 | 10 | 1 | 9 |
5.00 J/cm2 | 10 | 9 | 1 |
According to the test, the damage threshold of the mirror was 2.00 J/cm2 (532 nm, 10 ns pulse, 10 Hz, Ø0.803 mm). Please keep in mind that these tests are performed on clean optics, as dirt and contamination can significantly lower the damage threshold of a component. While the test results are only representative of one coating run, Thorlabs specifies damage threshold values that account for coating variances.
Continuous Wave and Long-Pulse Lasers
When an optic is damaged by a continuous wave (CW) laser, it is usually due to the melting of the surface as a result of absorbing the laser's energy or damage to the optical coating (antireflection) [1]. Pulsed lasers with pulse lengths longer than 1 µs can be treated as CW lasers for LIDT discussions.
When pulse lengths are between 1 ns and 1 µs, laser-induced damage can occur either because of absorption or a dielectric breakdown (therefore, a user must check both CW and pulsed LIDT). Absorption is either due to an intrinsic property of the optic or due to surface irregularities; thus LIDT values are only valid for optics meeting or exceeding the surface quality specifications given by a manufacturer. While many optics can handle high power CW lasers, cemented (e.g., achromatic doublets) or highly absorptive (e.g., ND filters) optics tend to have lower CW damage thresholds. These lower thresholds are due to absorption or scattering in the cement or metal coating.
LIDT in linear power density vs. pulse length and spot size. For long pulses to CW, linear power density becomes a constant with spot size. This graph was obtained from [1].
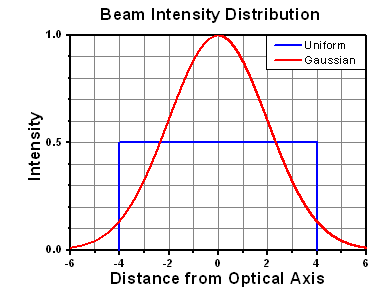
Pulsed lasers with high pulse repetition frequencies (PRF) may behave similarly to CW beams. Unfortunately, this is highly dependent on factors such as absorption and thermal diffusivity, so there is no reliable method for determining when a high PRF laser will damage an optic due to thermal effects. For beams with a high PRF both the average and peak powers must be compared to the equivalent CW power. Additionally, for highly transparent materials, there is little to no drop in the LIDT with increasing PRF.
In order to use the specified CW damage threshold of an optic, it is necessary to know the following:
- Wavelength of your laser
- Beam diameter of your beam (1/e2)
- Approximate intensity profile of your beam (e.g., Gaussian)
- Linear power density of your beam (total power divided by 1/e2 beam diameter)
Thorlabs expresses LIDT for CW lasers as a linear power density measured in W/cm. In this regime, the LIDT given as a linear power density can be applied to any beam diameter; one does not need to compute an adjusted LIDT to adjust for changes in spot size, as demonstrated by the graph to the right. Average linear power density can be calculated using the equation below.
The calculation above assumes a uniform beam intensity profile. You must now consider hotspots in the beam or other non-uniform intensity profiles and roughly calculate a maximum power density. For reference, a Gaussian beam typically has a maximum power density that is twice that of the uniform beam (see lower right).
Now compare the maximum power density to that which is specified as the LIDT for the optic. If the optic was tested at a wavelength other than your operating wavelength, the damage threshold must be scaled appropriately. A good rule of thumb is that the damage threshold has a linear relationship with wavelength such that as you move to shorter wavelengths, the damage threshold decreases (i.e., a LIDT of 10 W/cm at 1310 nm scales to 5 W/cm at 655 nm):
While this rule of thumb provides a general trend, it is not a quantitative analysis of LIDT vs wavelength. In CW applications, for instance, damage scales more strongly with absorption in the coating and substrate, which does not necessarily scale well with wavelength. While the above procedure provides a good rule of thumb for LIDT values, please contact Tech Support if your wavelength is different from the specified LIDT wavelength. If your power density is less than the adjusted LIDT of the optic, then the optic should work for your application.
Please note that we have a buffer built in between the specified damage thresholds online and the tests which we have done, which accommodates variation between batches. Upon request, we can provide individual test information and a testing certificate. The damage analysis will be carried out on a similar optic (customer's optic will not be damaged). Testing may result in additional costs or lead times. Contact Tech Support for more information.
Pulsed Lasers
As previously stated, pulsed lasers typically induce a different type of damage to the optic than CW lasers. Pulsed lasers often do not heat the optic enough to damage it; instead, pulsed lasers produce strong electric fields capable of inducing dielectric breakdown in the material. Unfortunately, it can be very difficult to compare the LIDT specification of an optic to your laser. There are multiple regimes in which a pulsed laser can damage an optic and this is based on the laser's pulse length. The highlighted columns in the table below outline the relevant pulse lengths for our specified LIDT values.
Pulses shorter than 10-9 s cannot be compared to our specified LIDT values with much reliability. In this ultra-short-pulse regime various mechanics, such as multiphoton-avalanche ionization, take over as the predominate damage mechanism [2]. In contrast, pulses between 10-7 s and 10-4 s may cause damage to an optic either because of dielectric breakdown or thermal effects. This means that both CW and pulsed damage thresholds must be compared to the laser beam to determine whether the optic is suitable for your application.
Pulse Duration | t < 10-9 s | 10-9 < t < 10-7 s | 10-7 < t < 10-4 s | t > 10-4 s |
---|---|---|---|---|
Damage Mechanism | Avalanche Ionization | Dielectric Breakdown | Dielectric Breakdown or Thermal | Thermal |
Relevant Damage Specification | No Comparison (See Above) | Pulsed | Pulsed and CW | CW |
When comparing an LIDT specified for a pulsed laser to your laser, it is essential to know the following:
LIDT in energy density vs. pulse length and spot size. For short pulses, energy density becomes a constant with spot size. This graph was obtained from [1].
- Wavelength of your laser
- Energy density of your beam (total energy divided by 1/e2 area)
- Pulse length of your laser
- Pulse repetition frequency (prf) of your laser
- Beam diameter of your laser (1/e2 )
- Approximate intensity profile of your beam (e.g., Gaussian)
The energy density of your beam should be calculated in terms of J/cm2. The graph to the right shows why expressing the LIDT as an energy density provides the best metric for short pulse sources. In this regime, the LIDT given as an energy density can be applied to any beam diameter; one does not need to compute an adjusted LIDT to adjust for changes in spot size. This calculation assumes a uniform beam intensity profile. You must now adjust this energy density to account for hotspots or other nonuniform intensity profiles and roughly calculate a maximum energy density. For reference a Gaussian beam typically has a maximum energy density that is twice that of the 1/e2 beam.
Now compare the maximum energy density to that which is specified as the LIDT for the optic. If the optic was tested at a wavelength other than your operating wavelength, the damage threshold must be scaled appropriately [3]. A good rule of thumb is that the damage threshold has an inverse square root relationship with wavelength such that as you move to shorter wavelengths, the damage threshold decreases (i.e., a LIDT of 1 J/cm2 at 1064 nm scales to 0.7 J/cm2 at 532 nm):
You now have a wavelength-adjusted energy density, which you will use in the following step.
Beam diameter is also important to know when comparing damage thresholds. While the LIDT, when expressed in units of J/cm², scales independently of spot size; large beam sizes are more likely to illuminate a larger number of defects which can lead to greater variances in the LIDT [4]. For data presented here, a <1 mm beam size was used to measure the LIDT. For beams sizes greater than 5 mm, the LIDT (J/cm2) will not scale independently of beam diameter due to the larger size beam exposing more defects.
The pulse length must now be compensated for. The longer the pulse duration, the more energy the optic can handle. For pulse widths between 1 - 100 ns, an approximation is as follows:
Use this formula to calculate the Adjusted LIDT for an optic based on your pulse length. If your maximum energy density is less than this adjusted LIDT maximum energy density, then the optic should be suitable for your application. Keep in mind that this calculation is only used for pulses between 10-9 s and 10-7 s. For pulses between 10-7 s and 10-4 s, the CW LIDT must also be checked before deeming the optic appropriate for your application.
Please note that we have a buffer built in between the specified damage thresholds online and the tests which we have done, which accommodates variation between batches. Upon request, we can provide individual test information and a testing certificate. Contact Tech Support for more information.
[1] R. M. Wood, Optics and Laser Tech. 29, 517 (1998).
[2] Roger M. Wood, Laser-Induced Damage of Optical Materials (Institute of Physics Publishing, Philadelphia, PA, 2003).
[3] C. W. Carr et al., Phys. Rev. Lett. 91, 127402 (2003).
[4] N. Bloembergen, Appl. Opt. 12, 661 (1973).
In order to illustrate the process of determining whether a given laser system will damage an optic, a number of example calculations of laser induced damage threshold are given below. For assistance with performing similar calculations, we provide a spreadsheet calculator that can be downloaded by clicking the LIDT Calculator button. To use the calculator, enter the specified LIDT value of the optic under consideration and the relevant parameters of your laser system in the green boxes. The spreadsheet will then calculate a linear power density for CW and pulsed systems, as well as an energy density value for pulsed systems. These values are used to calculate adjusted, scaled LIDT values for the optics based on accepted scaling laws. This calculator assumes a Gaussian beam profile, so a correction factor must be introduced for other beam shapes (uniform, etc.). The LIDT scaling laws are determined from empirical relationships; their accuracy is not guaranteed. Remember that absorption by optics or coatings can significantly reduce LIDT in some spectral regions. These LIDT values are not valid for ultrashort pulses less than one nanosecond in duration.
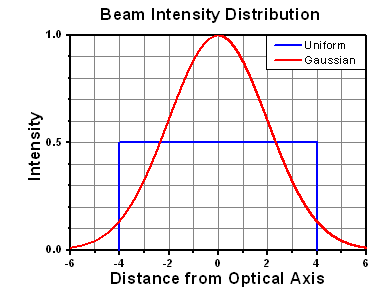
Figure 71A A Gaussian beam profile has about twice the maximum intensity of a uniform beam profile.
CW Laser Example
Suppose that a CW laser system at 1319 nm produces a 0.5 W Gaussian beam that has a 1/e2 diameter of 10 mm. A naive calculation of the average linear power density of this beam would yield a value of 0.5 W/cm, given by the total power divided by the beam diameter:
However, the maximum power density of a Gaussian beam is about twice the maximum power density of a uniform beam, as shown in Figure 71A. Therefore, a more accurate determination of the maximum linear power density of the system is 1 W/cm.
An AC127-030-C achromatic doublet lens has a specified CW LIDT of 350 W/cm, as tested at 1550 nm. CW damage threshold values typically scale directly with the wavelength of the laser source, so this yields an adjusted LIDT value:
The adjusted LIDT value of 350 W/cm x (1319 nm / 1550 nm) = 298 W/cm is significantly higher than the calculated maximum linear power density of the laser system, so it would be safe to use this doublet lens for this application.
Pulsed Nanosecond Laser Example: Scaling for Different Pulse Durations
Suppose that a pulsed Nd:YAG laser system is frequency tripled to produce a 10 Hz output, consisting of 2 ns output pulses at 355 nm, each with 1 J of energy, in a Gaussian beam with a 1.9 cm beam diameter (1/e2). The average energy density of each pulse is found by dividing the pulse energy by the beam area:
As described above, the maximum energy density of a Gaussian beam is about twice the average energy density. So, the maximum energy density of this beam is ~0.7 J/cm2.
The energy density of the beam can be compared to the LIDT values of 1 J/cm2 and 3.5 J/cm2 for a BB1-E01 broadband dielectric mirror and an NB1-K08 Nd:YAG laser line mirror, respectively. Both of these LIDT values, while measured at 355 nm, were determined with a 10 ns pulsed laser at 10 Hz. Therefore, an adjustment must be applied for the shorter pulse duration of the system under consideration. As described on the previous tab, LIDT values in the nanosecond pulse regime scale with the square root of the laser pulse duration:
This adjustment factor results in LIDT values of 0.45 J/cm2 for the BB1-E01 broadband mirror and 1.6 J/cm2 for the Nd:YAG laser line mirror, which are to be compared with the 0.7 J/cm2 maximum energy density of the beam. While the broadband mirror would likely be damaged by the laser, the more specialized laser line mirror is appropriate for use with this system.
Pulsed Nanosecond Laser Example: Scaling for Different Wavelengths
Suppose that a pulsed laser system emits 10 ns pulses at 2.5 Hz, each with 100 mJ of energy at 1064 nm in a 16 mm diameter beam (1/e2) that must be attenuated with a neutral density filter. For a Gaussian output, these specifications result in a maximum energy density of 0.1 J/cm2. The damage threshold of an NDUV10A Ø25 mm, OD 1.0, reflective neutral density filter is 0.05 J/cm2 for 10 ns pulses at 355 nm, while the damage threshold of the similar NE10A absorptive filter is 10 J/cm2 for 10 ns pulses at 532 nm. As described on the previous tab, the LIDT value of an optic scales with the square root of the wavelength in the nanosecond pulse regime:
This scaling gives adjusted LIDT values of 0.08 J/cm2 for the reflective filter and 14 J/cm2 for the absorptive filter. In this case, the absorptive filter is the best choice in order to avoid optical damage.
Pulsed Microsecond Laser Example
Consider a laser system that produces 1 µs pulses, each containing 150 µJ of energy at a repetition rate of 50 kHz, resulting in a relatively high duty cycle of 5%. This system falls somewhere between the regimes of CW and pulsed laser induced damage, and could potentially damage an optic by mechanisms associated with either regime. As a result, both CW and pulsed LIDT values must be compared to the properties of the laser system to ensure safe operation.
If this relatively long-pulse laser emits a Gaussian 12.7 mm diameter beam (1/e2) at 980 nm, then the resulting output has a linear power density of 5.9 W/cm and an energy density of 1.2 x 10-4 J/cm2 per pulse. This can be compared to the LIDT values for a WPQ10E-980 polymer zero-order quarter-wave plate, which are 5 W/cm for CW radiation at 810 nm and 5 J/cm2 for a 10 ns pulse at 810 nm. As before, the CW LIDT of the optic scales linearly with the laser wavelength, resulting in an adjusted CW value of 6 W/cm at 980 nm. On the other hand, the pulsed LIDT scales with the square root of the laser wavelength and the square root of the pulse duration, resulting in an adjusted value of 55 J/cm2 for a 1 µs pulse at 980 nm. The pulsed LIDT of the optic is significantly greater than the energy density of the laser pulse, so individual pulses will not damage the wave plate. However, the large average linear power density of the laser system may cause thermal damage to the optic, much like a high-power CW beam.
Posted Comments: | |
No Comments Posted |

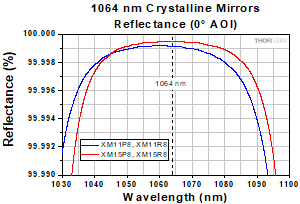
Click to Enlarge
Click Here for Theoretical Data From 800 - 1500 nm
Theoretical Reflectance of 1064 nm Crystalline Supermirrors
- Plano or Concave (1 m Radius of Curvature) Supermirrors with 1064 nm Center Wavelength
- Finesse in a Two-Mirror System:
- 100 000 (Item #s: XM11P8 and XM11R8)
- 200 000 (Item #s: XM15P8 and XM15R8)
- Optical Absorption: <1 ppm Typical*
- Optical Scatter: <5 ppm Typical*
- XM15x8 Mirrors have Coatings Designed for Low Thermo-Optic (TO) Noise
- For Complete Specifications, See the Specs Tab Above
Thorlabs offers plano and concave supermirrors featuring Ø8 mm crystalline coatings on Ø1" UVFS substrates with extremely high reflectance at the center wavelength of 1064 nm. The concave mirrors are designed with a 1 m radius of curvature. The XM11P8 and XM11R8 mirrors feature 100 000 finesse and reflectance >99.9969%, while the XM15P8 and XM15R8 mirrors feature 200 000 finesse and reflectance >99.9984%.
The XM15P8 and XM15R8 mirrors use a new thermo-optic-noise-optimized multilayer design that allows for a lower thermal noise contribution from the crystalline coating. Coherent cancellation between the thermo-elastic (TE) noise and thermo-refractive (TR) noise contributions of the coating is achieved through optimization of the coating layer structure. This results in a TO-noise contribution lower than both the individual Brownian noise and stubstrate TE noise. For more details on the TO-noise optimization, please see "Coherent cancellation of photothermal noise in GaAs/Al0.92Ga0.08As Bragg mirrors" by Tara Chalermsongsak et al.** We also have partnered with Wolfram® to create a web application that allows you to directly compare the optical cavity noise performance between our TO-optimized crystalline coating and conventional ion-beam sputtered (IBS) coatings for a variety of cavity design parameters. The application may be accessed by clicking the link here: Optical Cavity Noise Comparison Tool.
To download test data on a purchased item, click the Item # below, and enter its serial number in the "Download Serial Item Data" box.
*Mirrors with optical absorption <1 ppm and optical scatter <5 ppm are available upon request. Contact Tech Support for more information.
**Chalermsongsak T, Hall ED, Cole GD, Follman D, Seifert F, Arai K, Gustafson EK, Smith JR, Aspelmeyer M, and Adhikari RX. "Coherent cancellation of photothermal noise in GaAs/Al0.92Ga0.08As Bragg mirrors."Metrologia. March 9, 2016; 53: 860-868.

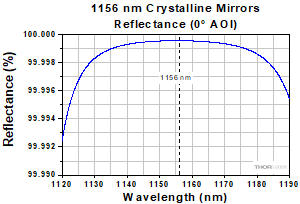
Click to Enlarge
Click Here for Theoretical Data From 800 - 1500 nm
Theoretical Reflectance of 1156 nm Crystalline Supermirrors
- Plano or Concave (1 m Radius of Curvature) Supermirrors with 1156 nm Center Wavelength
- Finesse in a Two-Mirror System: 300 000
- Optimal for Frequency Doubling 1156 nm to the Ytterbium Clock Transition at 578 nm
- Optical Absorption: <1 ppm Typical*
- Optical Scatter: <5 ppm Typical*
- For Complete Specifications, See the Specs Tab Above
Thorlabs offers plano and concave supermirrors featuring Ø8 mm crystalline coatings on Ø1" UVFS substrates with >99.999% reflectance at the center wavelength of 1156 nm. The concave mirrors are designed with a 1 m radius of curvature.
To download test data on a purchased item, click the Item # below, and enter its serial number in the "Download Serial Item Data" box.
*Mirrors with optical absorption <1 ppm and optical scatter <5 ppm are available upon request. Contact Tech Support for more information.

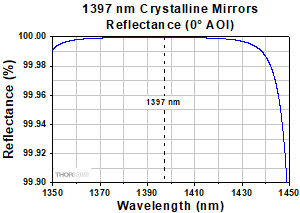
Click to Enlarge
Click Here for Theoretical Data From 900 - 1900 nm
Theoretical Reflectance of 1397 nm Crystalline Supermirrors
- Plano or Concave (1 m Radius of Curvature) Supermirrors with 1397 nm Center Wavelength
- Finesse in a Two-Mirror System: 300 000
- Optimal for Frequency Doubling 1397 nm to the Strontium Clock Transition at 698 nm
- Optical Absorption: <1 ppm Typical*
- Optical Scatter: <5 ppm Typical*
- For Complete Specifications, See the Specs Tab Above
Thorlabs offers plano and concave supermirrors featuring Ø8 mm crystalline coatings on Ø1" IRFS substrates with >99.999% reflectance at the center wavelength of 1397 nm. The concave mirrors are designed with a 1 m radius of curvature.
To download test data on a purchased item, click the Item # below, and enter its serial number in the "Download Serial Item Data" box.
*Mirrors with optical absorption <1 ppm and optical scatter <5 ppm are available upon request. Contact Tech Support for more information.

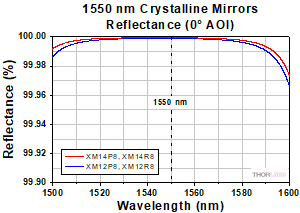
Click to Enlarge
Click Here for Theoretical Data From 1000 - 2000 nm
Theoretical Reflectance of 1550 nm Crystalline Supermirrors
- Plano or Concave (1 m Radius of Curvature) Supermirrors with 1550 nm Center Wavelength
- Finesse in a Two-Mirror System:
- 200 000 (Item #s: XM12P8 and XM12R8)
- 300 000 (Item #s: XM14P8 and XM14R8)
- Optical Absorption: <1 ppm Typical*
- Optical Scatter: <5 ppm Typical*
- For Complete Specifications, See the Specs Tab Above
Thorlabs offers plano and concave supermirrors featuring Ø8 mm crystalline coatings on Ø1" UVFS substrates with extremely high reflectance at the center wavelength of 1550 nm. The concave mirrors are designed with a 1 m radius of curvature. The XM12P8 and XM12R8 mirrors feature 200 000 finesse and reflectance > 99.9984%, while the XM14P8 and XM14R8 mirrors feature 300 000 finesse and reflectance > 99.999%.
To download test data on a purchased item, click the Item # below, and enter its serial number in the "Download Serial Item Data" box.
*Mirrors with optical absorption <1 ppm and optical scatter <5 ppm are available upon request. Contact Tech Support for more information.

Specifications | ||
---|---|---|
Material | Premium Grade ULE®* | |
Clear Aperturea | Chamfer to Through Hole | |
Side of Optic | Front Sidea | Back Side |
Surface Flatness | <λ/4 at 633 nm | Commercial Polish |
Surface Quality |
20-10 Scratch Dig | Commercial Polish |
- Stabilize Zero-Crossing Temperature of Coefficient of Thermal Expansion
- Compensate for Flexure from Spacers
This Ø1" compensation ring, also known as a backing ring, is fabricated from ultra-low-expansion glass and features a Ø9 mm through hole. The front side of the ring, indicated by the polished bevel, can be contacted to the back of our crystalline mirrors. Doing so ensures that the zero-crossing temperature of the coefficient of thermal expansion of the entire cavity remains at or around room temperature and also compensates for the flexure when the mirrors are contacted to a spacer to form an optical cavity.
For those wishing to use this compensation ring with other fused silica mirrors, note that the coating diameter on the face of the substrate to be contacted to the ring should either be small enough to fit completely inside or at least as large as the outer diameter of the ring.
*ULE is a registered trademark of Corning, Inc.