Multi-Position Sliders with Resonant Piezoelectric Motors
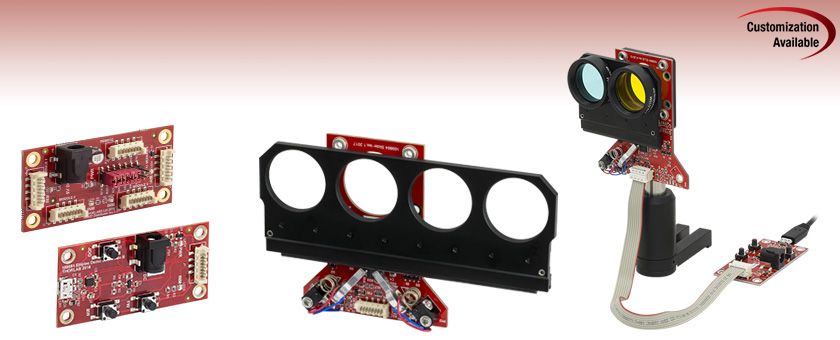
- Mount Multiple SM05- or SM1-Threaded Components
- Open Frame Design for OEM Applications
- Control via Interface Board, GUI, or ASCII Message Calls
- Fully Integrated Drive Electronics
Application Idea
ELL6K Bundle Components Shown Assembled, with Two Colored Glass Filters, and Mounted Using the ELLA1 Adapter
Four-Position Slider
(Also Available Individually)
Interface Board
ELL9K
Four-Position
Slider Bundle
(Board and Slider Included)
ELLB
Bus Distributor

Please Wait
Key Specsa | |||
---|---|---|---|
Item # | ELL12(K) | ELL6(K) | ELL9(K) |
Ports for Mounted Optics | Six, SM05 Threaded | Two, SM1 Threaded | Four, SM1 Threaded |
Switching Time Range | No Load: 350 to 400 ms 150 g Load: <600 ms |
No Load: 180 to 270 ms 100 g Load: <600 ms |
No Load: 450 to 500 ms 150 g Load: <700 ms |
Positioning Repeatability | <100 µm (30 µm Typical) | ||
Maximum Total Loadb | 150 g (5.29 oz) | ||
DC Voltage Input | 4.5 to 5.5 V | ||
Weight (Slider Only) | 78.5 g (2.77 oz) | 44.0 g (1.55 oz) | 70.0 g (2.47 oz) |
Minimum Lifetimec | 3.3 Million Operations or 100 km Total Travel |
Elliptec Resonant Motor Products | |||||
---|---|---|---|---|---|
![]() |
![]() |
![]() |
![]() |
![]() |
![]() |
Multi-Position Sliders | 28 mm Linear Stage | 60 mm Linear Stage | Rotation Stage | Rotation Mount | Motorized Iris |
Features
- Ideal for OEMs and Applications Requiring Rapid Switching
- Micro-B USB and Picoflex®1 Connectors for Control Signals
- Multi-Drop Serial Communication Protocol Supported
- SM05- or SM1-Threaded Ports for Mounted Optics or Other Components
- Photo-Interrupter Optical Sensor Technology for Precise Positioning
- Compatible with 30 mm Cage System Components
- Bus Distributor, Post Mount Adapter, and Accessory Upgrade Pack Available Below
Thorlabs offers multi-position sliders with millisecond switching times enabled by Thorlabs' Elliptec® piezoelectric resonant motor technology. Each slider is available as a standalone unit as well as in a complete package that include an interface board. Thorlabs also offers accessory packs, which can be used to upgrade standalone units to complete kits. Our compact and lightweight multi-position sliders all use the same custom-designed PCB, with the ELL6 featuring one motor and the ELL12 and ELL9 including two. The motors are highly dynamic and have no gearing. As the motor includes no magnets, it is compatible with
The open frame format, versatility, and simplicity of these sliders make them attractive for OEM applications, as they can be customized according to customer requirements and produced in high-volume quantities. Please see our OEM and Manufacturing Capabilities page for more information.
Control
There are multiple options for powering, driving, and controlling these multi-position sliders, which are detailed in the Slider Operation section of the Operation tab. Each slider possesses a 3.3 V serial bus and is designed to be operated with or without the interface board; the Pin Diagram tab provides pin assignments. Thorlabs offers software for our Elliptec products capable of providing full and independent control of the slider. When the interface board is used as an accessory to change the position of the carriage on the slider, the carriage's status in the software is automatically updated. Please note that the dual-position and four-position sliders are not designed for continuous operation. We recommend operation with duty cycles of 40% or less.
Multiple Elliptec devices can be controlled using the ELLB Bus Distributor or by splicing multiple connectors onto one ribbon cable. A single bus distributor can connect up to four Elliptec devices; up to 16 devices can be connected if the buses are daisy chained. This bus can be controlled one of three ways: through an interface board (included with the bundles below) connected to a PC running the Elliptec software, by connecting to an Arduino®2 or Raspberry Pi®3 board, or by wiring the connector pins to a user-supplied control board. Alternatively, up to 16 devices can be spliced onto a single ribbon cord, at which point the devices can be simultaneously controlled by the interface board or selectively controlled by the Elliptec software. See the manual for instruction on how to splice multiple devices onto a ribbon cord and the Pin Diagrams tab for pin assignments when making custom connections.
Application Idea
The multi-position sliders are well suited as filter changers, and the ELL6 is also recommended as shutter. Their carriages feature SM05- or SM1-threaded bores with 3.5 mm deep threads, and four
- Picoflex is a registered trademark of Molex Incorporated.
- Arduino is a registered trademark of Arduino Sa Société Anonym (SA).
- Raspberry Pi is a registered trademark of the Raspberry Pi Foundation.
Specifications
Performance specifications are given for the case when the multi-position slider is mounted as recommended in the Operation tab.
Item # | ELL12(K) | ELL6(K) | ELL9(K) | |
---|---|---|---|---|
Performance | ||||
Switching Time between Adjacent Positions |
Unloaded Carriage on Slider | 350 to 400 ms | 180 to 270 ms | 450 to 500 ms |
Loaded Carriage on Slider | <600 ms (150 g Load) | <600 ms (100 g Load) | <700 ms (150 g Load) | |
Thread Type of Ports in Carriage | Internal SM05 (0.535"-40)a Threads, 3.5 mm Deep |
Internal SM1 (1.035"-40)a Threads, 3.5 mm Deep | ||
Number of Threaded Ports in Carriage | Six | Two | Four | |
Travel | 95 mm (3.74") | 31 mm (1.22") | 93 mm (3.66") | |
Positioning Repeatabilityb | <100 µm (30 µm Typical) | |||
Maximum Total Load (Vertically Mounted)c | 150 g (5.29 oz) | |||
Minimum Lifetimed | 3.3 Million Switching Operations or 100 km Total Travel | |||
Electrical | ||||
DC Voltage Input | 4.5 to 5.5 V | |||
Typical Current Consumption |
During Movement | <1200 mA | <600 mA | <1200 mA |
During Standby | 38 mA | |||
During Search for Resonant Frequenciese |
1.2 A | |||
Communications | ||||
Busf | Multi-Drop 3.3 V/5 V TTL RS232 | |||
Connector on Multi-Position Slider Board | Picoflex® | |||
Connectors on Interface Board | Picoflex® Micro-B USB 5 VDC Power: [For Plug with Ø5.5 mm OD (Ground) and Ø2.1 mm ID (+5 V)] |
|||
Speed | 9600 baud/s | |||
Data Lengthg | 8 bit | |||
Protocol Data Format | ASCII HEX | |||
Module Address and Command Format | Mnemonic Character | |||
8-Conductor Ribbon Cable Length | Supplied: 0.250 m; Max: 3 m | |||
Mechanical | ||||
Dimensions of the Slider (At End Stops)h | 143.5 mm x 77.7 mm x 14.2 mm (5.65" x 3.06" x 0.56") |
80.5 mm x 77.7 mm x 14.9 mm (3.16" x 3.06" x 0.59") |
143.5 mm x 77.7 mm x 14.9 mm (5.65" x 3.06" x 0.59") |
|
Dimensions of the Interface Board | 32.0 mm x 66.0 mm x 12.5 mm (1.26" x 2.60" x 0.49") |
|||
Weight (Slider) | 78.5 g (2.77 oz) | 44.0 g (1.55 oz) | 70.0 g (2.47 oz) | |
Weight (Interface Board) | 10.3 g (0.36 oz) | |||
Environmental Operating Conditions | ||||
Temperature Range | 15 to 40 °C | |||
Maximum Relative Humidity (Non-Condensing) | <80% at 31 °C | |||
Maximum Altitude | 2000 m |
ELL12 & ELL9 Connector J2 Pinouta,b | ||
---|---|---|
Pin | Type | Function |
1 | PWR | Ground |
2 | OUT | OTDX - Open Drain Transmit 3.3 V TTL RS232 |
3 | IN | RX Receive 3.3 V TTL RS232 |
4 | OUT | In Motion, Open Drain Active Low Max 5 mA |
5 | IN | JOG/Mode, Active Low Max 5 V |
6 | IN | BW Backward, Active Low Max 5 V |
7 | IN | FW Forward, Active Low Max 5 V |
8 | PWR | VCC +5 V ± 10%; 1200 mA |
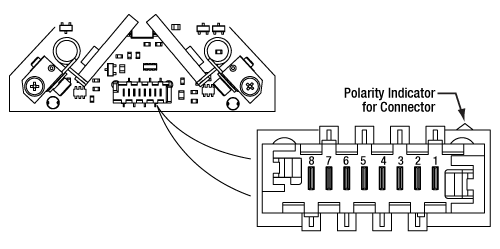
Click to Enlarge
Pinout diagram of the Picoflex® connector is shown referenced to a partial diagram
of the ELL12 and ELL9 slider board. The polarity indicator on the connector
must be adjacent to the red wire on the supplied 8-connector cable.
ELL6 Connector J2 Pinouta,b | ||
---|---|---|
Pin | Type | Function |
1 | PWR | Ground |
2 | OUT | OTDX - Open Drain Transmit 3.3 V TTL RS232 |
3 | IN | RX Receive 3.3 V TTL RS232 |
4 | OUT | In Motion, Open Drain Active Low Max 5 mA |
5 | IN | JOG/Mode = Normal/Test Demo, Active Low Max 5 V |
6 | IN | BW Backward, Active Low Max 5 V |
7 | IN | FW Forward, Active Low Max 5 V |
8 | PWR | VCC +5 V ± 10%; 600 mA |
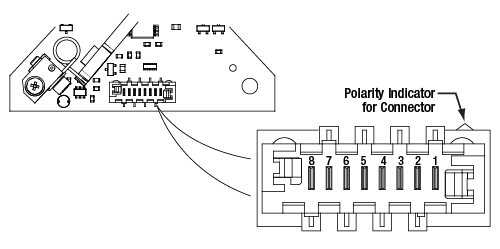
Click to Enlarge
Pinout diagram of the Picoflex® connector is shown referenced to a partial diagram
of the ELL6 slider board. The polarity indicator on the connector
must be adjacent to the red wire on the supplied 8-connector cable.
ELLB Connector J1, J2, J3, and J4 Pinouta,b | ||
---|---|---|
Pin | Type | Function |
1 | PWR | Ground |
2 | OUT | OTDX - Open Drain Transmit 3.3 V TTL RS232 |
3 | IN | RX Receive 3.3 V TTL RS232 |
4 | OUT | In Motion, Open Drain Active Low Max 5 mA |
5 | IN | Not Connected |
6 | IN | Not Connected |
7 | IN | Not Connected |
8 | PWR | VCC +5 V ± 10%; 800 mA per Connected Device |
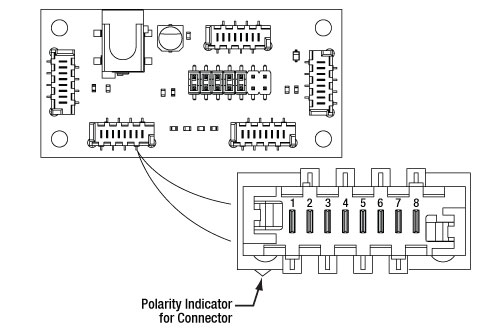
Click to Enlarge
Pinout diagram of the Picoflex® connector is shown referenced to a simplified diagram
of the ELLB Bus Distributor. The polarity indicator on the connector
must be adjacent to the red wire on the supplied 8-connector cables.
Operation Notes
This tab contains information on handling, mounting, and operating these multi-position sliders.
Contents- Handling
- Mounting
- Loading
- Supplying Power
- Operation of the Motor
- Resonant Frequencies
- Slider Operation
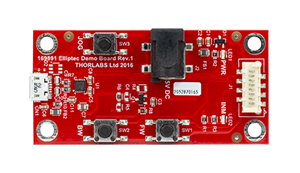
Click to Enlarge
Figure 2 The Interface Board
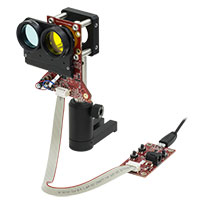
Click to Enlarge
Figure 4 ELL6K with Glass Filters and Mounted using 30 mm Cage System Components
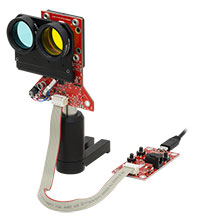
Click to Enlarge
Figure 3 ELL6K with Glass Filters and Mounted using the ELLA1
Handling
Our sliders and interface boards are robust to general handling. An assembled ELL9K bundle with labels indicating key features is shown in Figure 1, and a picture of an interface board is in Figure 2. To ensure reliable operation, keep the surface contacted by the motor free of oils, dirt, and dust. It is not necessary to wear gloves while handling the dual-position or four-position slider, but avoid touching the surface contacted by the motor to avoid transferring contaminants to it. If it is necessary to clean the surface contacted by the motor, it can be wiped using KW32 or similar extra low lint sheets and isopropyl alcohol or mineral spirits (white spirit). Do not use acetone, as this solvent will damage the plastic edge of the slider's carriage.
The open frame format of these sliders can tolerate up to 8 kV of static discharge. ESD precautions should be taken, as an electrostatic discharge can produce an electrical signal that may cause an unintended movement of the carriage. Avoid subjecting the structural PCB to loads in excess of 500 g. If an excessive load is applied the PCB may bend, which will degrade the performance of the slider.
Mounting
These multi-position sliders may be operated with the slider mounted vertically (upright) or horizontally (laying down), assuming certain conditions are met. When the slider is oriented vertically, ensure that the carriage translates side-to-side, rather than up-and-down, as the effects of gravity substantially reduce the maximum load that may be translated. When it is mounted vertically, the slider may be oriented with the motor(s) above or below the carriage. The recommended orientation is with the motor(s) below the carriage, as is shown in Figures 3 - 7, which minimizes the chance of any dust or particulates displaced during operation settling on the surface of the optics mounted in the carriage. When mounting the slider horizontally, ensure that the installation does not bend the PCB. In all cases, do not allow anything to interfere with moving parts of the slider and make sure that the slider and the mounted optics are secure to avoid jostling during motion.
There are several options for mounting the sliders. The ELLA1 Post Mount Adapter, which is available below, fastens directly to the back of the slider's PCB. As shown in Figure 3, the adapter can then be used to mount the slider to a Ø1/2" post. The compact dimensions of the ELLA1 allows sliders to be placed one behind the other while minimizing the space separating them, as shown below. The adapter can also be integrated with Thorlabs' 30 mm Cage System components and/or SM1-threaded components, such as lens tubes. Alternately, 30 mm cage system components alone can be used to mount the sliders. An example of this is shown in Figure 4, in which a CP33 Cage Plate, four ER1 rods, a Ø1/2" post, and a post holder mount and support the assembled ELL6K.
Loading
The maximum total load specification of 150 g refers to the weight of the load mounted to the carriage, and does not include the weight of the slider. For example, the weight of the unloaded ELL6 slider is approximately 22 g, and the maximum allowed weight of the mounted components is 150 g; the combined maximum permitted weight of the slider and mounted components is 172 g. The sliders are designed to be compatible with 30 mm cage system components.
Supplying Power
Using the Interface Board
Even though ultrasonic voltage signals are required to operate the motors, the stage is powered by applying a DC voltage signal to the interface board. The electronics on the board, which convert the applied DC signal to a sinusoidal signal oscillating at the desired resonant frequency, make this possible.
The ELL6 includes one motor and the ELL12 and ELL9 include two. Because of the lower power requirements of the ELL6's single motor, it is possible to supply power to the ELL6 through the Micro-B USB connector on the interface board. A 5 V power supply is not included in the ELL6K bundle. Operation of sliders with two motors requires a 5 V power supply, and one is included in the ELL12K and ELL9K bundles.
An advantage of powering the ELL6 using the Micro-B USB connector on the interface board is that a computer can be used to simultaneously control and power the slider. Laptops can supply the amperage necessary to enable switching between positions on the ELL6 dual-position slider; however, some laptops may not be able to supply the 1.2 A required to perform a search for optimal resonant frequencies, which is described in the following Resonant Frequencies section. When this is the case, and it is necessary to perform a search for optimal resonant frequencies, an alternate power source capable of delivering the needed amperage must be used to supplement the power provided by the laptop.
When the setup includes the ELL12 or ELL9 and an interface board, power is supplied through the 5 VDC power socket. As the Micro-B USB connector does not supply power sufficient to drive both motors, this connector is used only for computer control of the slider.
Without the Interface Board
When these sliders are incorporated into an application without the interface board, the connection with the power source is made using the pins on the Picoflex® connector. A pinout diagram of this connector is included in the Pin Diagram tab, and information on powering and addressing the slider given in its manual and the communications protocol manual respectively.
Operational Principle of the Motor
The Elliptec motors move the carriages on the sliders between positions, and the direction of the translation is determined by the ultrasonic frequency driving motor's piezoelectric elements. For each motor, there is one ultrasonic resonant frequency that will push the carriage forward, and another that will pull the carriage backward. Operating a motor at one of its resonance frequencies causes the tip of the motor to continuously cycle in a tight clockwise elliptical path. When the motor is driven at its other resonance frequency, the tip of the motor cycles through that same path in a counterclockwise direction. Both resonance frequencies are around 100 kHz. The total displacement at the tip of motor is a function of the mechanical load it is driving and the voltage supplied to the piezo element. In the case of no loading and a 5 V maximum driving voltage at a resonant frequency, the tip of the motor expands and contracts no more than a few microns while tracing the elliptical path. Please see The Elliptec® Motor tab for more information and an animation that illustrates the operational principle of the motor.
Resonance Frequencies
On power-up, the factory default setting instructs the slider to search for the resonance frequencies that will deliver the best performance. During this process, the slider will translate between the forward and backward positions. At the conclusion of this calibration process, the slider is in the backward position. If this movement on start-up is undesirable, it is possible to disable this calibration procedure by using the serial port to initialize the frequencies on power-up. A new search for optimal resonance frequencies may be performed at any time; to maintain optimal performance, it is recommended that new searches be performed after changes in loading and/or ambient temperature. Please see Section Section 4.4 of the manual for details.
Slider Operation
Note that our sliders are not intended for continuous operation. We recommend operation with duty cycles of less than 40% during general use, while operation with duty cycles greater than 60% should be limited to a few seconds.
The movement of the slider's carriage may be controlled by pressing buttons on the interface board, through computer control via the Elliptec® software package that may be downloaded, or by sending simple signals to digital lines on the slider board. The constant drive power results in a linear speed profile, which enables the motor to accelerate and decelerate in a few microseconds.
The interface board may be used as an accessory while interfacing with the slider through the Elliptec software; all changes in the position of the carriage that occur as a result of pressing buttons on the interface board are registered by the software, and the software may independently control the carriage while the interface board is connected. The buttons on the interface board can be seen in Figure 2.
Multiple Elliptec devices can be be controlled using the ELLB Bus Distributor or by splicing multiple connectors onto one ribbon cable. A single bus distributor can connect up to four Elliptec devices; up to 16 devices can be connected if the buses are daisy chained. This bus can be controlled one of three ways: through an interface board (included with the bundles below) to connect to a PC running the Elliptec software, by connecting to an Arduino® or Raspberry Pi® board, or by wiring the connector pins to a user-supplied control board. Note that if an interface board is used, its on-unit buttons will be disabled. Alternatively, up to 16 devices can be spliced onto a single ribbon cord. The devices can then be simultaneously controlled by the interface board or selectively controlled by the Elliptec software. See the manual for instruction on how to splice multiple devices onto a ribbon cord and the Pin Diagrams tab for pin assignments when making custom connections. The communications protocol manual describes how to use the software to individually address each connected device. A link to download the software and accompanying documentation can be found in the Software tab.
Figures 5 - 7, as well as the animation included on the Overview tab, show the operation of the ELL6 slider using the interface board. By pressing the button on the interface board marked 'FW,' as is about to be done in Figure 6, the slider is sent to the forward position. The slider will return to the home position when the button on the interface board marked 'BW' is pressed.
When using the interface board to control the position of the carriage on the ELL12 or ELL9 sliders, the JOG button is also used. If the slider is facing forward and oriented vertically with motors beneath the translating mount, press and hold the JOG button then press the FW button to move the carriage one position to the observer's right. Press and hold the JOG button and press the BW button to move the carriage one position to the observer's left.
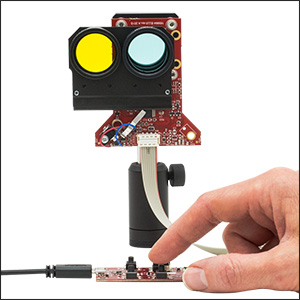
Click to Enlarge
Figure 6 The carriage will translate from the backward
position (Figure 5 and above) to the forward position
(Figure 7) in response to a press of the FW button.
ELL12K and ELL9K Slider Bundles
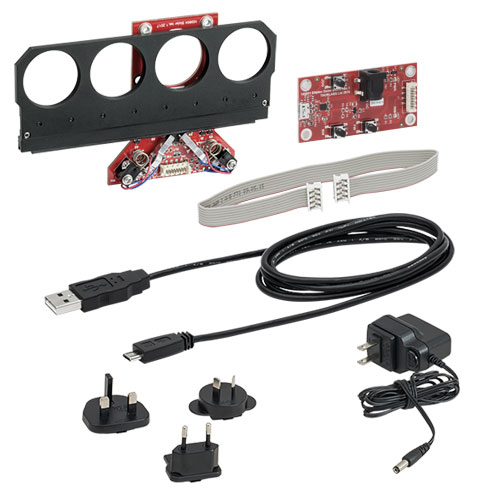
Click to Enlarge
Components of the ELL9K Bundle
One Region-Specific Power Adapter Included, All Region-Specific Plugs Shown for Reference
Each Bundle Includes the Following:
- Slider
- Interface Board
- Micro-B to A-Type USB Cable
- 8-Conductor 28 AWG Ribbon Cable
- 5 V Power Supply with Location-Specific Plug
PC-based software is also available for download, as are the manual, communications protocol manual, and other documentation.
ELL6K Slider Bundle

Click to Enlarge
Components of the ELL6K Bundle
Each Bundle Includes the Following:
- Slider
- Interface Board
- Micro-B to A-Type USB Cable
- 8-Conductor 28 AWG Ribbon Cable
PC-based software is also available for download, as are the manual, communications protocol manual, and other documentation.
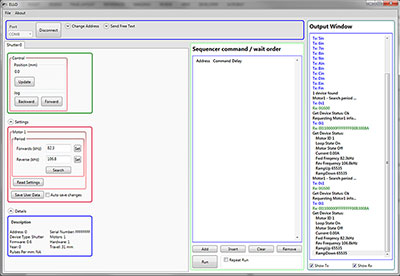
Click to Enlarge
The Elliptec Piezoelectric Resonant Motor Control Software GUI
Software for Devices Driven by Elliptec® Piezoelectric Resonant Motors
All devices based on the Elliptec® resonant piezo motor may be controlled by the Elliptec system software, which features an intuitive graphical user interface (GUI). The source code, in C# format, is included in software bundle available for download, and custom applications can be created in any language. The image at right shows a screen capture of the GUI, and the button that follows links to the download page.
Commands are entered in the Sequencer command / wait order section located at the center-left of the GUI. An example of a sequence of commands that might be sent to the device is "Afw" to move the slider at address "A" to the forward position and then "Abw" to move the slider at address "A" to the backward position. The command "As1" is used to perform the frequency search that will identify the optimal resonant frequencies, for the current operating conditions, for the motor at address "A."
SM05 Threading: Ø1/2" Lens Tubes, 16 mm Cage Systems | |||
---|---|---|---|
External Thread, 0.535"-40.0 UNS-2A | Internal Thread, 0.535"-40.0 UNS-2B | ||
Max Major Diameter | 0.5340" | Min Major Diameter | 0.5350" |
Min Major Diameter | 0.5289" | Min Pitch Diameter | 0.5188" |
Max Pitch Diameter | 0.5178" | Max Pitch Diameter | 0.5230" |
Min Pitch Diameter | 0.5146" | Min Minor Diameter (and 83.3% of Thread) | 0.508" |
Max Minor Diameter | 0.5069" | Max Minor Diameter (and 64.9% of Thread) | 0.514" |
RMS Threading: Objective, Scan, and Tube Lenses | |||
---|---|---|---|
External Thread, 0.800"-36.0 UNS-2A | Internal Thread, 0.800"-36.0 UNS-2B | ||
Max Major Diameter | 0.7989" | Min Major Diameter | 0.8000" |
Min Major Diameter | 0.7934" | Min Pitch Diameter | 0.7820" |
Max Pitch Diameter | 0.7809" | Max Pitch Diameter | 0.7866" |
Min Pitch Diameter | 0.7774" | Min Minor Diameter (and 83.3% of Thread) | 0.770" |
Max Minor Diameter | 0.7688" | Max Minor Diameter (and 64.9% of Thread) | 0.777" |
C-Mount Threading: Machine Vision Lenses, CCD/CMOS Cameras | |||
---|---|---|---|
External Thread, 1.000"-32.0 UN-2A | Internal Thread, 1.000"-32.0 UN-2B | ||
Max Major Diameter | 0.9989" | Min Major Diameter | 1.0000" |
Min Major Diameter | 0.9929" | Min Pitch Diameter | 0.9797" |
Max Pitch Diameter | 0.9786" | Max Pitch Diameter | 0.9846" |
Min Pitch Diameter | 0.9748" | Min Minor Diameter (and 83.3% of Thread) | 0.966" |
Max Minor Diameter | 0.9651" | Max Minor Diameter (and 64.9% of Thread) | 0.974" |
SM1 Threading: Ø1" Lens Tubes, 30 mm Cage Systems | |||
---|---|---|---|
External Thread, 1.035"-40.0 UNS-2A | Internal Thread, 1.035"-40.0 UNS-2B | ||
Max Major Diameter | 1.0339" | Min Major Diameter | 1.0350" |
Min Major Diameter | 1.0288" | Min Pitch Diameter | 1.0188" |
Max Pitch Diameter | 1.0177" | Max Pitch Diameter | 1.0234" |
Min Pitch Diameter | 1.0142" | Min Minor Diameter (and 83.3% of Thread) | 1.008" |
Max Minor Diameter | 1.0068" | Max Minor Diameter (and 64.9% of Thread) | 1.014" |
SM30 Threading: Ø30 mm Lens Tubes | |||
---|---|---|---|
External Thread, M30.5 x 0.5 – 6H/6g | Internal Thread, M30.5 x 0.5 – 6H/6g | ||
Max Major Diameter | 30.480 mm | Min Major Diameter | 30.500 mm |
Min Major Diameter | 30.371 mm | Min Pitch Diameter | 30.175 mm |
Max Pitch Diameter | 30.155 mm | Max Pitch Diameter | 30.302 mm |
Min Pitch Diameter | 30.059 mm | Min Minor Diameter (and 83.3% of Thread) | 29.959 mm |
Max Minor Diameter | 29.938 mm | Max Minor Diameter (and 64.9% of Thread) | 30.094 mm |
SM1.5 Threading: Ø1.5" Lens Tubes | |||
---|---|---|---|
External Thread, 1.535"-40 UNS-2A | Internal Thread, 1.535"-40 UNS-2B | ||
Max Major Diameter | 1.5339" | Min Major Diameter | 1.535" |
Min Major Diameter | 1.5288" | Min Pitch Diameter | 1.5188" |
Max Pitch Diameter | 1.5177" | Max Pitch Diameter | 1.5236" |
Min Pitch Diameter | 1.5140" | Min Minor Diameter (and 83.3% of Thread) | 1.508" |
Max Minor Diameter | 1.5068" | Max Minor Diameter (and 64.9% of Thread) | 1.514" |
SM2 Threading: Ø2" Lens Tubes, 60 mm Cage Systems | |||
---|---|---|---|
External Thread, 2.035"-40.0 UNS-2A | Internal Thread, 2.035"-40.0 UNS-2B | ||
Max Major Diameter | 2.0338" | Min Major Diameter | 2.0350" |
Min Major Diameter | 2.0287" | Min Pitch Diameter | 2.0188" |
Max Pitch Diameter | 2.0176" | Max Pitch Diameter | 2.0239" |
Min Pitch Diameter | 2.0137" | Min Minor Diameter (and 83.3% of Thread) | 2.008" |
Max Minor Diameter | 2.0067" | Max Minor Diameter (and 64.9% of Thread) | 2.014" |
SM3 Threading: Ø3" Lens Tubes | |||
---|---|---|---|
External Thread, 3.035"-40.0 UNS-2A | Internal Thread, 3.035"-40.0 UNS-2B | ||
Max Major Diameter | 3.0337" | Min Major Diameter | 3.0350" |
Min Major Diameter | 3.0286" | Min Pitch Diameter | 3.0188" |
Max Pitch Diameter | 3.0175" | Max Pitch Diameter | 3.0242" |
Min Pitch Diameter | 3.0133" | Min Minor Diameter (and 83.3% of Thread) | 3.008" |
Max Minor Diameter | 3.0066" | Max Minor Diameter (and 64.9% of Thread) | 3.014" |
SM4 Threading: Ø4" Lens Tubes | |||
---|---|---|---|
External Thread, 4.035"-40 UNS-2A | Internal Thread, 4.035"-40.0 UNS-2B | ||
Max Major Diameter | 4.0337" | Min Major Diameter | 4.0350" |
Min Major Diameter | 4.0286" | Min Pitch Diameter | 4.0188" |
Max Pitch Diameter | 4.0175" | Max Pitch Diameter | 4.0245" |
Min Pitch Diameter | 4.0131" | Min Minor Diameter (and 83.3% of Thread) | 4.008" |
Max Minor Diameter | 4.0066" | Max Minor Diameter (and 64.9% of Thread) | 4.014" |
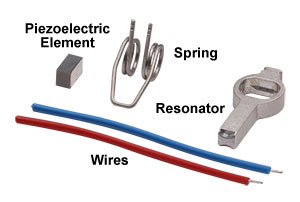
Click to Enlarge
The Components of the Elliptec Motor

Click to Enlarge
The Elliptec Piezoelectric Resonant Motor
The Elliptec® Piezoelectric Resonant Motor
Thorlabs' Elliptec® piezo resonant motor, shown at right, is lightweight, with a mass of 1.2 g, and compact: the dimensions of the resonator housing, excluding the spring, are 8 mm x 4 mm x 20 mm.
Components of the Motor
The components that compose the motor are shown at far-right. The piezoelectric element is press fit into the aluminum resonator, which has been precisely designed and machined to produce the desired elliptical motion at the tip and to interface optimally with the driven module. The free ends of the spring are integrated with the resonator housing. The wires, which are soldered to the top and bottom of the piezoelectric element, deliver the voltage signal that induces the piezoelectric element to vibrate at ultrasonic frequencies.
When the motor is built into a system, the open loop of the spring is bolted to a sturdy surface that is stationary with respect to the item to be driven, and the tip of the resonator is placed in contact with the item. The purpose of the spring is to maintain constant contact between the tip of the resonator and the driven item, and the direction of motion is determined by the resonance frequency at which the piezo element is driven.
Elliptical Motion and Comparison with Conventional Motors
The motor is operated by driving it at one of its two resonance frequencies. A voltage signal oscillating at an ultrasonic frequency is applied to the piezoelectric chip, which responds by expanding less than a micron and then contracting back to its original dimensions at the frequency of the driving signal. This rapid-cycling change in the chip's dimensions causes a vibration in the aluminum resonator housing. When the vibration is at one of the housing's resonance frequencies, a pushing motion results at the tip of the motor. When the vibration is at the other resonance frequency a pulling motion results.
As illustrated in the video, the pulling and pushing motions result from the tip of the motor tracing an elliptical path in space when the motor operates at resonance. The selected resonance frequency controls the direction of the cyclical motion. The motor's tip traces one half of the ellipse as it expands and the other half as it contracts. When the motor pushes the driven item, the motor's tip is in contact with the item while the tip expands; the two are not in contact while the tip contracts. The converse is true when the motor pulls the driven item in the opposite direction. The total displacement at the tip of the motor is a function of both the mechanical load it is driving and the voltage supplied to the piezo element. The maximum displacement can be up to a few microns when the peak driving voltage is 5 V.
The motor behaves in many ways like a DC or electromagnetic stepper motor, but it does not suffer from many of the drawbacks of these conventional motors. Unlike conventional electromagnetic motors, which must overcome inertial delays to come to a stop, the highly dynamic Elliptec motor can stop within microseconds. As it has no gears, it does not exhibit backlash. Since it possesses no magnets, it is compatible with use in environments sensitive to electromagnetic interference. The motion of the driven element is continuous and smooth. As the tip of the motor must be in contact with the driven item to induce motion, the motor possesses the safety feature of an inherent friction brake. When in contact with a plastic surface, the motor operates virtually silently.
For OEM applications, the motor can be manufactured in volume at low cost, and it can be driven by inexpensive analog electronics. It does not require microprocessors or software; however it is compatible for use with them.
Posted Comments: | |
user
 (posted 2024-09-05 12:59:04.92) Hi, is there an easy way to disconnect the drive channel wires? it feels hard and I do not want to damage the boards. spolineni
 (posted 2024-09-10 06:19:02.0) Thank you for reaching out. To safely disconnect the drive channel ribbon cables, ensure the connector is properly aligned with the header, with the polarity indicator matching the red wire. This will help avoid any damage to the board. I’ll contact you directly for further assistance. Zsolt Kis
 (posted 2024-06-28 12:22:18.5) Dear Support Team,
I have a question about the ELLB board. According to the user manual, one can attach more than one motor to the ELLB board one-by-one, changing always the address of the last added motor in the GUI and disconnecting-reconnecting the interface board. I would like to use two motors in a measurement setup, so I would like to avoid doing the above procedure each time when using (turning on) the measurement setup. How can I do this? If I controlled ELLB via a microcontroller through the RS232 port would this solve the problem?
Best regards
Zsolt Kis bwuensch
 (posted 2024-07-08 06:24:32.0) Thank you for reaching out to us.
You can save the address of the motor in the software so that you do not need to change it every time you connect it again.
I will reach out to you directly to discuss this further. Andreas B
 (posted 2024-06-14 13:22:24.04) Hi,
We are trying to operate a ELL9 slider together with two ELL14 rotators using a single interface board and a ELLB bus distributor. When we connect only the slider the device can be operated using the ELLO software. However when we connect more than one device, we start getting errors. Either the software says it cannot find any device or it seems to find devices but gives an error about not being able to divide by zero. Is this an issue you are familiar with and have any ideas for solutions? do'neill
 (posted 2024-06-20 08:54:14.0) Thank you for you comment. There can be a few issues that cause this but often it is due to multiple devices trying to connect on the same address. This address can be changed in the ELLO software. I will reach out to you directly to further troubleshoot this with you. Harrison Truscott
 (posted 2024-06-12 12:04:51.737) Hi, I seem to be having the same issue as Kirill Mitrofanov below - the board is at a point where it gets stuck halfway. This is inconsistent, and in the past it has been able to recovery via frequency search / repeated driving of the board, but as of a week ago it's been resistant to both. I've also tried cleaning it with IPA, to no effect. It's mostly a problem in the FW direction, though it does pause on the way back. Is there anything else I can try? spolineni
 (posted 2024-06-20 07:48:39.0) Thank you for reaching out to us. I apologize for the inconvenience you are experiencing with the ELL6. Please be assured that I will personally get in touch with you to provide further assistance in troubleshooting this issue. Gary Sevison
 (posted 2024-05-24 13:43:11.87) May I please get the labview example VI sent to me? Thanks! do'neill
 (posted 2024-06-03 07:29:20.0) Thank you for reaching out. I will contact you directly with example VIs for these stages. user
 (posted 2024-01-23 21:25:36.603) Hi,
I purchased a couple of rotation mounts (ELL14K and ELL18) for use with a high power femtosecond laser. I would like to have a protective cage to avoid damaging the electronic components and scattering of the laser. Do you have an example of a 3D printable design for this purpose?
Best regards. Bin Yang
 (posted 2023-12-29 07:35:01.76) I am trying to use LabView to control ELL9K. Can you please send me the example VI for that. Thank you! do'neill
 (posted 2024-01-04 08:46:18.0) Thank you for your enquiry. I will reach out to you directly to provide this example VI. Kirill Mitrofanov
 (posted 2023-12-20 12:42:58.02) I use ELL6 in my lab and at some point I got the following issue: the motor moves only half-distance and stops there. It looks like it tries to move more, but something stops it from doing that.
Is there any solution for that? do'neill
 (posted 2024-01-03 06:22:38.0) Thank you for your feedback and I am sorry to hear this. Usually this can be fixed by performing a frequency search, as operating too far from this optimum frequency can cause it to move slowly or not reach the desired location. The other thing I would suggest is to clean the rail with IPA as this can be another reason it does not reach the desired location. I will reach out to you directly to further help troubleshoot this with you. Fabian C
 (posted 2023-12-15 16:19:36.24) Hi
I currently have an ELL20K/M and ELL14K/M connected through the ELLB bus, and i would like to control them both with python. I have downloaded the example EEL17_pythonnet.py, but the problem is that the program moves both of them simultaneously. How can i avoid this to have independent control? Thanks do'neill
 (posted 2024-01-02 10:46:56.0) Thank you for your enquiry. This is possible with some editing of the example. As long as the devices are on different addresses, they can be controlled independently. I will reach out to you directly to help you through this. user
 (posted 2023-12-07 13:29:49.057) Hi, i want to control several devices using the ELLB bus and the software ELLO. When i scan the port, it recognized one device but nothing else shows. How can i send instructions to the different devices now? (this used to work when each device was connected separately, without using the ELLB)
Thanks Andreas B
 (posted 2023-11-06 11:06:29.717) Hi, We bought an Elliptec multi-positioner filter mount. It worked fine to start with but now suddenly gives "Sensor error". Any thought on how to adress this issue? do'neill
 (posted 2023-11-13 04:45:37.0) Response from Daniel at Thorlabs. This is caused by the motor not reaching the correct position or not being able to sense the starting position. One of the first things you can do is frequency scan the device and gently and carefully clean the rail with IPA. I will reach out to you directly to troubleshoot this with you. Alex B
 (posted 2023-09-17 23:13:49.947) Hello, I would also like to use the LabVIEW drivers. Can you send them to me too? Thanks do'neill
 (posted 2023-09-19 07:21:08.0) Response from Daniel at Thorlabs. We do not have LabVIEW wrappers or drivers for the Elliptec stages but the .NET DLLs that are included with ELLO install. I will reach out to you with an example VI to get you started. Stephan Troyer
 (posted 2023-08-04 12:43:47.94) In the ELLB's manual it could be useful to note that the USB RX/TX pins work as UART. Many things are quite obvious in hindsight, but when having issues (for example since the board is not responding any command when no motor is connected or when receiving garbage from a floating), that confirmation would be useful as a confirmation.
In addition, it is noteworthy, that TX/RX is reversed compared to common labelling. Usually, TX of one device gets connected to RX of the other device. On the distributor port, one has to connect the microcontroller's TX pin to the distributor board's TX pin. The naming gets slightly inconsistent since the board's TX pin is internally connected to the RX pin of the MOLEX connector.
Since it's not only the manual but also the PCB where the TX/RX labelling is printed, I would at least clearly specify the mix up it in the manual.
Best,
Stephan Troyer fguzman
 (posted 2023-08-08 05:16:54.0) Thanks for your feedback. We have taken note on this and we will revise your comments on this. Ralf Wunderlich
 (posted 2023-06-13 17:22:09.523) Hi,
I am using your ELL6K in a box that also houses an APD. When I connect the ELL6K to the USB port (providing power to the device), I have a significant increase in the APD's count rate? Most likely the ELL6K is using optical position feedback from an LED or something. Can you specify the wavelength?
Kind regards do'neill
 (posted 2023-06-21 06:55:39.0) Response from Daniel at Thorlabs. The home sensor of the device uses a 950nm led which can leak light. This should be taken into consideration for environments that are sensitive to light sources at and around this wavelength. Kai M
 (posted 2023-05-31 18:12:13.823) Hi, I'm using ELLB to control multiple ELL14. How do I set multiple devices properly in ELLO software? Could you also share Labview VI for controlling multiple devices using ELLB? Thank you! do'neill
 (posted 2023-06-02 12:32:52.0) Response from Daniel at Thorlabs. I will reach out to you directly to provide these VIs and help you with your application. user
 (posted 2023-04-11 18:46:31.413) Do you happen to have an example VI (LabView) written for this device available? If yes, could you please share where we can locate it? Many thanks! JReeder
 (posted 2023-04-12 03:20:59.0) Thank you for your enquiry. I have reached out to you directly to provide an example LabVIEW VI for this product. user
 (posted 2023-01-19 16:39:36.737) Hi, you state that the ELL series sliders should not be mounted such that the carriage moves vertically, only horizontally. Will they work if they are mounted "upside down" i.e. such that the carriage moves horizontally but the motor being above the carriage? JReeder
 (posted 2023-01-20 11:52:00.0) Thank you for your enquiry. This is not something we have tested extensively, but we believe that this should work. It is worth noting though that the ELLx devices produce some fine particulates due to the friction mechanism which in this orientation can drop down onto the optics. Takahiro Deguchi
 (posted 2023-01-19 14:29:55.29) Dear Thorlabs
We purchased ELL9K and installed in our single molecule microscope. Recently, we found out that ELL9 (not the interface board) emits some kind of light so that it was giving a high amount of background to our camera images. By adding short-pass 750 filter in front of camera, we could block the background signal completely. Do you know if there is any LED or a light source in IR on ELL9?
I just wanted to know if you are aware of this or if it is specified somewhere. Thank you.
Best regards
Takahiro DEGUCHI JReeder
 (posted 2023-01-20 05:35:24.0) Thank you for your enquiry. All of our ELLx devices use a photo interrupter for the homing and encoder, it emits at 950 nm and the detector part is sensitive from 700 to 1200 nm. Due to this light source, applications that are very sensitive to 950 nm light should not use the ELLx devices or should take precautions to protect their application from this light. Some ELL devices may also struggle to home if they are exposed to a large amount of light in the 700-1200 nm range. user
 (posted 2023-01-08 01:41:06.937) Is there any example VI (labview) written for this device? If so, where can we find it? Thank you! do'neill
 (posted 2023-01-10 11:25:04.0) Response from Daniel at Thorlabs. Thank you for your inquiry. We will get in touch with you directly. Yannic Staechelin
 (posted 2022-12-16 09:11:57.787) I use your ELL9 in an optical setup, where it changes its position every five seconds for some hours. In the beginning it works just fine, but after some time a "Sensor Error" occurs repeatedly. Is there anything I can do to avoid the "Sensor Error"? cwright
 (posted 2022-12-16 10:24:26.0) Response from Charles at Thorlabs: Thank you for your query. These sensors are small IR LEDs paired with photodiodes. When paddles on the back of the moving world block the light from hitting the photodiode, the position of the stage is updated. Sensor errors are usually the result of ambient light/laser light getting into the photodiode, dust obscuring the photodiode, or a paddle not sufficiently blocking the light. I will reach out to you to help resolve this. Lavonne Dettmers
 (posted 2022-11-08 12:27:05.457) Could you please allow the ELL9 to be generated on a RoHS compliance certificate?
Thanks,
Lavonne Dettmers cwright
 (posted 2022-11-14 05:20:22.0) Response from Charles at Thorlabs: Thank you for your query. A member of technical support will look into this and reach out to you by email. Tao Ding
 (posted 2022-11-04 13:26:05.6) can it be controlled via serial port?do you provide the reference code? cwright
 (posted 2022-11-04 10:29:23.0) Response from Charles at Thorlabs: Thank you for your query. These devices can be controlled via serial over the USB port or by wiring directly to the relevant pins specified in the pin diagrams. THe command protocol can be found here: https://www.thorlabs.com/Software/Elliptec/Communications_Protocol/ELLx%20modules%20protocol%20manual.pdf c. Schmidt
 (posted 2022-10-05 13:43:21.087) Is there a way to limit/slow down the velocity and/or acceleration of ELL9? cwright
 (posted 2022-10-06 05:33:53.0) Response from Charles at Thorlabs: Thank you for your query. Unfortunately this is not possible with the filter sliders. The elliptec mounts are designed for quick positioning but not for control over the velocity parameters. Zihao Pang
 (posted 2022-05-12 22:13:36.01) Hi Thorlabs,
we've recently purchased the ELL14K Bundle. We are wondering if it is possible to make this rotator have continuous rotation for many full turns? For example, can this rotator keep jogging?
Many thanks and best regards,
Zihao cwright
 (posted 2022-05-13 04:33:45.0) Response from Charles at Thorlabs: Thank you for contacting us. The ELL14 is currently limited to 720 degrees of rotation by jogging. It is also possible to set non-stop continuous rotation at a slower speed and this is described in the communications protocol (https://www.thorlabs.com/Software/Elliptec/Communications_Protocol/ELLx%20modules%20protocol%20manual.pdf). I will reach out to discuss this with you. David Roesel
 (posted 2022-01-31 06:43:39.32) In case anyone is interested, we are writing a Python library for easy control of Elliptec devices. Feel free to reach out if you have any questions.
https://github.com/roesel/elliptec cwright
 (posted 2022-02-01 06:08:14.0) Response from Charles at Thorlabs: Thank you for contacting us! We think it's great to see the community engaging with our products and creating such libraries, although of course Thorlabs cannot take responsibility for the content and maintenance such community provided libraries. We are sure there is potential to benefit a number of people.research teams and will reach out to you to discuss your work. user
 (posted 2022-01-18 18:07:32.8) What is the Maximum Total Load in the horizontal movement mode? cwright
 (posted 2022-01-20 05:25:06.0) Response from Charles at Thorlabs: Thank you for your query. We would still suggest a maximum load of 150g in this configuration. Friedemann Heinz
 (posted 2021-12-09 11:47:10.013) Short comment:
It would be nice if the device would be "thinner". This could be realised by offering a slider with deeper threads such that a filter may be directly mounted in the slider without the use of additional lense tubes. There is actually a quite large gap betwenn slider and red electronic board.
Best,
Friedemann Heinz cwright
 (posted 2021-12-09 08:04:12.0) Response from Charles at Thorlabs: Thank you for your feedback! I can see how this would be advantageous and will post your feedback on our internal forums for our engineers to contemplate. user
 (posted 2021-11-08 09:03:48.587) Is it possible to perform small movements within one sample, i.e. not a full sample jump? cwright
 (posted 2021-11-08 11:11:30.0) Response from Charles at Thorlabs: Thank you for your query. Unfortunately this is not possible. I would suggest using an ELL17/M or ELL20/M and positioning an optic mount such as LMR1/M on top. user
 (posted 2021-10-22 07:48:52.753) When using ELL6 or ELL9 products (and other USB stages), is it possible to use a USB hub (mains-powered) ?
ELL9 warns against having the component plugged in USB when a computer isn't fully on. What of a USB hub ? Can it be plugged as long as the hub is powered ? Should the cable be disconnected every time beofre we power off the computer or hub ? Under which conditions can we let an ELL stage connected ? cwright
 (posted 2021-11-01 11:42:33.0) Response from Charles at Thorlabs: Thank you for your query.
This was an issue with old versions of the USB remote interface board. Version 2 onwards should not have this issue. The issue is backfeeding of current to the USB hub. The way the USB has been implemented within the computer's USB HUB will determine whether or not it is suitable and our engineers found that even within the same laptop you could have some USB ports which are OK and will not be affected and others which are not OK and could have this issue. If using the old board then the only way to be sure is to either power the PC first or to desolder the transistor (labelled Q1 on the old boards). You cannot fix this with an external HUB. user
 (posted 2021-08-20 18:05:54.71) Is there any SDK or module to develop 3rd party software with python cwright
 (posted 2021-08-27 10:11:14.0) Response from Charles at Thorlabs: Thank you for your query. With Python we would recommend using the serial command protocol and I have reached out to you with an example which should get you started. The protocol is available here: https://www.thorlabs.de/Software/Elliptec/Communications_Protocol/ELLx%20modules%20protocol%20manual.pdf user
 (posted 2021-08-20 18:04:38.94) Is there any SDK or module to develop 3rd party software with python user
 (posted 2021-08-17 04:28:11.31) I think it should be stated more prominently (maybe on the main product page and not only in footnote (c) on the specs page) that the ELL9 can only be operated horizontally. When mounted on, e.g., a motorized rotation mount (which might be something a lot of customers think of as a possible application scenario), the ELL9 only moves correctly when aligned horizontally. In vertical orientation (rotation stage turned by 90 degrees), the motors are to weak to move even the weight of the slider alone, i.e., without any optics attached. Even though this might be obvious, it might still be a good idea to put a comment on the webpage.
In our case, we found a quick workaround, always turning the rotation mount before changing the ELL9 position, so that the slider motion always occurs in the horizontal direction. But other customers may want to use the slider at arbitrary rotation angles, which won't work out.
Apart from that, these are awesome devices. cwright
 (posted 2021-08-18 05:29:28.0) Response from Charles at Thorlabs: Thank you for your feedback. We will consider adding a clarifying note to the web presentation. The behaviour in this orientation is more due to the nature of the motor than its strength. The motor's tip follows an elliptical path when active and in order to advance the moving world it must leave contact with this moving world for a short time each repetition. When used with the slider orientated vertically the effect of gravity would oppose the intended motion of the slider and cause slipping. This motion can be seen in more detail in the video on the following page:
https://www.thorlabs.com/newgrouppage9.cfm?objectgroup_id=9464&tabname=The%20Elliptec%20Motor joe M
 (posted 2021-07-26 13:17:28.53) Hi,
I am hoping to control the ELL9K using labview (2017 32-bit). My computer is 64 bit and everytime I try to download the 32bit elliptec software so I can access the DLL I get an error saying I need an x86 processor. Can someone provide me with the DLL file? Also, is it possible to get example code for labview control?
Thanks cwright
 (posted 2021-07-27 10:47:41.0) Response from Charles at Thorlabs: Thank you for your query. If you have 32 bit LabVIEW on 64 bit windows then all your DLLs will need to be of 32 for 64 bit (WOW64) type. The Elliptec DLLs are only available as 64 bit or 32 bit. In this case you would need to have a 64 bit installation of LabVIEW or communicate with the Elliptec devices using serial commands. Technical support will reach out to you to discuss this. cwright
 (posted 2021-07-27 10:47:41.0) Response from Charles at Thorlabs: Thank you for your query. If you have 32 bit LabVIEW on 64 bit windows then all your DLLs will need to be of 32 for 64 bit (WOW64) type. The Elliptec DLLs are only available as 64 bit or 32 bit. In this case you would need to have a 64 bit installation of LabVIEW or communicate with the Elliptec devices using serial commands. Technical support will reach out to you to discuss this. Jiri Junek
 (posted 2021-07-23 04:56:18.707) Dear Thorlabs,
I want to use ELL14K and ELL17K/M in one optical setup. Am I need a Bus Distributor ELLB or can I control both devices separately? I plan to control the whole setup in Matlab.
Thank You for the information! cwright
 (posted 2021-07-23 06:36:12.0) Response from Charles at Thorlabs: Thank you for your query. You can control both separately. The ELLB is most suitable when you want to have many devices on a single USB port but you can use these two on separate USB ports and they will appear to your computer as two COM ports. I have reached out to you to discuss your application in more detail.
If using Matlab we would recommend you send serial commands according to our communication protocol: https://www.thorlabs.de/Software/Elliptec/Communications_Protocol/ELLx%20modules%20protocol%20manual.pdf Luis Mollinedo
 (posted 2021-05-11 06:30:42.76) Dear sir/madam,
We're interested in your Multi-Position Sliders with Resonant Piezoelectric Motors, specifically in your ELL9K bundle.
As we're planning to control the slider from an computer, running GNU/Linux OS (Ubuntu 20.04), is your software compatible with this OS? If not, is possible for us to develop our own driver (e.g. via serial communication).
Thanks in advance,
Luis Mollinedo
Robotics Lead
Overture Life
https://overture.life jcater
 (posted 2021-05-12 09:35:49.0) Response from Jack at Thorlabs: Thank you for your inquiry. Unfortunately our ELLO software is only compatible with Windows OS. You can communicate with the ELL9 through serial commands using the interface board or, for example, an Arduino or Raspberry Pi board, or by wiring the RX and TX connector pins to your own board. The command protocol can be found here https://www.thorlabs.com/Software/Elliptec/Communications_Protocol/ELLx%20modules%20protocol%20manual.pdf. Amit Meller
 (posted 2021-04-26 07:30:30.727) Hi,
It would be great if the ELL6K (as well as the other units in this line) will be ready to controlled using LabView, in a similar way to many of other Thorlabs products.
This unit is integrated in optomechanical prototypes or setups containing many elements and imaging devices and while the stand alone software is nice, it is not practical for full system integration.
Thank you
Amit Meller cwright
 (posted 2021-04-26 11:23:16.0) Response from Charles at Thorlabs: Thank you for your feedback. It is possible to use Elliptec devices in LabVIEW either by using the serial commands over VISA or by using the .NET DLL, detailed in the DLL which is downloaded with our software. By default it is found in the following loation: C:\Program Files\Thorlabs\Elliptec. The DLL is 64-bit, so your installation of LabVIEW would also need to be in order to use the DLL. For serial using VISA this is not important.
As you have opted not to be contacted by us please contact technical support if you have questions regarding this. jiang peng
 (posted 2021-04-20 12:38:38.79) Some bugs were mainly found. The resonant motor will produce auto-fluorescence after plugging in the USB, about 100kcounts/s, which is detected by APD (Single Photon Counter), which is very fatal for microscopic fluorescence testing and will cover up when scanning imaging. For weak light signals, a single nanoparticle is usually only 15k-40kcounts/s. James Grieve
 (posted 2021-03-11 20:38:22.797) When using the ELLB to control multiple stages over serial, is there any way to enumerate connected devices? The protocol manual is silent on this, mentioning only that the default address is '0'. cwright
 (posted 2021-03-11 09:51:46.0) Response from Charles at Thorlabs: Thank you for your query. When using multiple stages on the same COM port you will have to change their addresses by attaching one stage at a time. This can be done using the ELLO software through the "Change Address" option at the top of the program window and then saving the change by clicking Save User Data in the "Settings" panel.
Alternatively you can send the commands 0ca1, to change the address of a stage from 0 to 1, followed by the user save command to address 1, i.e. 1us. These are described in more detail in the command protocol document: https://www.thorlabs.com/Software/Elliptec/Communications_Protocol/ELLx%20modules%20protocol%20manual.pdf user
 (posted 2021-03-04 08:40:58.017) Hi, can I get example for LabVIEW (2018 32 bits) ?? Thanks cwright
 (posted 2021-03-09 08:11:03.0) Response from Charles at Thorlabs: Hello and thank you for your query. We will reach out to you about an example you can use. user
 (posted 2021-02-04 14:25:47.1) Hi, my ELL9 slider started mooving with difficulty, as its rail would need some oil or fat. What kind of oil/fat should I use? Thanks cwright
 (posted 2021-02-05 08:51:32.0) Response from Charles at Thorlabs: Hello and thank you for your query. By far the most common cause of movement issues are settings such as incorrect motor frequencies and you could try a frequency search. If there is a lot of dust/dirt which has entered the linear rail then you could try cleaning it with Ultrasol. Your local technical support team has already reached out to you. Naaman Amer
 (posted 2019-07-10 16:32:28.25) Hi
Can I use the device in Vacuum environment?
Can I control it via labview?
Thanks AManickavasagam
 (posted 2019-07-19 05:04:02.0) Response from Arunthathi at Thorlabs: Thanks for your query. Unfortunately, except for the motor itself the elliptic range is not vacuum compatible. This could be controlled with Labview (the .dll files would be in the installation folder). Peter Domenicali
 (posted 2019-05-22 00:56:54.707) Can the ELL6 be used long-term upside down? That is, with the bulk of its PC board pointing upwards, opposite to how it is shown in all your images? I should think one concern would be whether any wear particles will slough off of the friction interface, where the "inch worm" drive oscillates. If so these particles might drop down onto the optic being moved. But any other reason this wouldn't work? AManickavasagam
 (posted 2019-05-22 11:37:11.0) Response from Arunthathi at Thorlabs: Thanks for your query. The ELL6 should be perfectly fine to work in the flipped orientation you require. user
 (posted 2019-04-03 04:07:51.447) Hi Thorlabs service Team,
Nice little product. I am using the serial commands in python (pyserial) to access the four-position slider.
The connection is always successful and "0in" always returns the right output. Occasionally however, a "0ma00000000" is unsuccessful and returns a "signal error" - "0GS0A". Once it occurs, I can't move the stage anymore, even when I disconnect with python and connect with ELLO. (0ma attempts always return 0GS0A) Unplugging the stage resolves this issue but do you have any advice on how I could prevent this from happening?
Note: This never happened so far with the ELLO_DLL in python but I would prefer serial commands to keep the script more versatile. user
 (posted 2019-04-05 07:13:29.0) Response from Arunthathi at Thorlabs: Thanks for your query. The encoder error (0x0A) returned is a discrepancy between number of count position and requested position. It is generally a mechanical issue: vibration, moving load, stage moved or stopped by hand.
It is recommended to use HOME instead of “ma” to go to the 0 position.
Home resumes the unit from error (caused by vibration) as it resets the encoder to a known absolute 0 position.
If the issue still persists please contact your local tech support team directly for further assistance. Julien PROUST
 (posted 2019-03-26 11:28:40.167) I measured the stability:
Positioning Repeatability +/-0.26 mm in normal condition (vertical)
After around 30 actuations, a shift of 0.1 mm appears user
 (posted 2019-03-27 11:07:04.0) Response from Arunthathi at Thorlabs: Thanks for your feedback. To look into this further we will need to analyse your test setup and methods. I have contacted you directly for further details. user
 (posted 2019-02-12 15:45:57.423) I second: Would be awesome to have micromanager support! rmiron
 (posted 2019-02-14 05:41:42.0) Response from Radu at Thorlabs: Thank you for sharing your thoughts with us. I will relay your feedback internally. keisuke.yoshioka
 (posted 2018-11-04 21:21:15.983) ELL9Kで穴位置を細かく動かしたいのですが、maコマンドが使えないようでした。
maコマンドを使用できるように、仕様を変更して欲しいです。 rmiron
 (posted 2018-11-06 04:33:55.0) Response from Radu and Fumi at Thorlabs: この度はお問合せいただきありがとうございました。ご要望をファームウエア開発チームに伝え確認いたしました。"ma"コマンドや"mr"コマンドはELL9で使用することは自体は可能です。ただし、決められた4つのスライダーポジションに移動できるだけであり、精密な移動はできません。これは、他のElliptec製ステージと異なり、ELL9がエンコーダを搭載していないためであり、大変恐れ入りますがファームウエアの改造のみでは実現ができません。ただ、所定の時間に対してスムースに移動するようコマンドを送ることは可能です。そのようなコマンドに対するご質問や"ma"コマンドに対する応答についてのご質問がございましたら、弊社の日本オフィスsales@thorlabs.jpにご連絡くださいませ。
Translation:
Feedback: I want to finely move the hole positions with ELL9K, but it seems that the 'ma' (move absolute) command can not be used. I'd like for the stage to change such that we can use the 'ma' command.
Response: Thank you for your feedback. I have relayed it to the developers of Elliptec's firmware who will take it into account when planning for future releases. The 'ma' and 'mr' commands can be used on ELL9, but only to switch between the 4 slider positions. Unfortunately, we can't modify this stage's firmware in order to allow these commands to be used for fine translations. This is because ELL9, as opposed to the other Elliptec stages, lacks an encoder. With that being said, we could add a similar command that would allow one to translate the stage for a given period of time. If your stage is not responding to the 'ma' or 'mr' commands, please contact our Japanese office at sales@thorlabs.jp. lvjing
 (posted 2018-04-19 14:52:34.907) Usb plugged in the computer can not identify the device bhallewell
 (posted 2018-04-19 12:21:32.0) Response from Ben at Thorlabs: Thank you for your email. I'll contact you to troubleshoot the problem. massimo
 (posted 2018-03-29 14:55:49.94) Is it possible to turn off the LEDs in the interface board?
I'm using this slider to move ND filters and my optical setup is enclosed in a light tight box, because I need to perform measurement at very low light. The flat cable between the interface board and the slider is too short so I have to keep the interface board inside the light controlled box, but the light intensity of the LED on the board is not at all negligible. At the moment I'm covering the LED with black tape, but it's definitely not enough and not very nice.
I couldn't find anything about it in the documentation. It'd be great if didn't have to replace the flat cable with a longer one.
Thanks bhallewell
 (posted 2018-04-05 07:19:20.0) Response from Ben at Thorlabs: Thank you for your feedback. There isn't a programming solution to turn off the LED however you should have access to remove the LED or alternatively short the LED with a wire. user
 (posted 2018-03-27 17:29:38.03) It would be awesome if this had drivers for micro manager. rmiron
 (posted 2018-04-11 05:16:53.0) Response from Radu at Thorlabs: Thank you for your feedback. I have relayed it to our developers. I will contact you directly regarding our future plans on this front. Roger.John
 (posted 2018-02-15 22:01:57.177) Can one mount a ME1-P01 in one position of the ELL6, as a flip mirror alternative? Thanks! bhallewell
 (posted 2018-02-23 10:55:22.0) Response from Ben at Thorlabs: You will be able to mount this optic through use of our SM1L03 SM1 Lens tube, which includes an SM1RR retaining ring to secure the optic in the lens tube. The optic seated in the lens tube can then be threaded into the ELL6 mount. The total load that the slider can actuate is 0.150 kg. user
 (posted 2017-10-25 15:33:18.65) Could the ELL6 be used in a medium vacuum (>10^-2mbar) environment? Thank you very much. bwood
 (posted 2017-10-30 05:06:50.0) Response from Ben at Thorlabs: Thank you for your feedback. While in principle the Elliptec motor technology will work in a vacuum, the stock ELL6 slider contains several components which will outgas, so it may not be suitable for your application. If you would like to pursue this further, I would suggest contacting your local tech support office, to discuss your application in more detail. nhuffman
 (posted 2017-07-25 10:20:39.697) Are there any 32bit libraries for the Eliptec software available for 64bit Windows like are available for the APT and Kinesis software? I need to interface with 32bit MATLAB on a 64bit machine. bwood
 (posted 2017-07-26 09:27:16.0) Response from Ben at Thorlabs: Thank you for your question. Unlike Kinesis compatible devices, our Elliptec devices are controlled solely through serial commands (directly or through our Elliptec System Software). You should be able to configure MatLab to communicate through these serial commands however. You can find the serial communications protocol on the Elliptec software webpage. bjorn.fjelddahl
 (posted 2016-11-29 08:32:55.62) Hi
The ELL6 is made for 2 filters
Is it possible to add two more filters to a total of 4?
Best regards,
Björn bhallewell
 (posted 2016-12-01 07:23:58.0) Response from Ben at Thorlabs: Thank you for your enquiry. This would likely fall within our capabilities for customisation. I will contact you to discuss this opportunity further. user
 (posted 2016-11-04 16:04:37.99) Do the top two threaded hole have clearance from the sliding portion to attach 30 cage posts on each side? i.e. can you stack multiples of these? bhallewell
 (posted 2016-11-09 09:39:00.0) Response from Ben at Thorlabs: Thank you for your question here. Checking our web models, there is not enough clearance for an ER 30mm cage rod system to mate with the PCB from both sides, this is a 4-40 hole which can only be accessed from the rear side. This is one of our off-the-shelf solutions & is limited in customisation however for OEM opportunities we may be able to go beyond this. I will contact you directly to start a discussion. |


Click to Enlarge
Red and blue wires deliver power to the motor, whose aluminum tip contacts the edge of the carriage. During operation, the motor's tip cycles at ultrasonic speeds and on a microscopic scale. Its movement cannot be seen by the human eye.
- Bundle is Ideal for OEM Evaluation Testing
- Easy Integration into a Setup
- Operate using Manual and/or Computer Control
These multi-position slider bundles are complete kits that include the slider, also available separately, and the other components listed in the table below. The ELL6, with its single motor, can be simultaneously controlled and powered via USB. As the two motors on the ELL12 and ELL9 sliders require greater power, a 5 V power supply is included with their respective kits.
These packages facilitate quick integration of the slider into laboratory setups and other experimental applications. They also provides a convenient means to evaluate integrated this technology into OEM applications.
Kit Components | |||
---|---|---|---|
Item # | Slider | Accessories | Power Supply |
ELL12K | ELL12 Slider with Six SM05-Threaded Ports |
Interface Board, USB Cable, Ribbon Cable (8-Conductor, 28 AWG) |
5 V Power Supply with Region-Specific Plug |
ELL6K | ELL6 Slider with Two SM1-Threaded Ports |
- | |
ELL9K | ELL9 Slider with Four SM1-Threaded Ports |
5 V Power Supply with Region-Specific Plug |

Item # | # of Ports | Port Thread |
---|---|---|
ELL12 | 6 | SM05 (0.535"-40) |
ELL6 | 2 | SM1 (1.035"-40) |
ELL9 | 4 |
- Standalone Multi-Position Sliders with SM05 or SM1-Threaded Ports
- Command the Slider by Connecting through an Existing Interface Board or Directly via the Multidrop TTL RS-232 Interface
- Serves Applications that do not Require an Interface Board or Cables
- Can be Used to Expand an Existing Network of Elliptec® Devices
These multi-position sliders are offered as standalone products. They are frequently used to meet the needs of applications whose design requires multiple networked Elliptec® resonant motor products, or applications that do not require the other components included in the bundles above. Each position on the carriage has an SM05- or SM1-threaded bore with 3.5 mm deep threads. The four
The PCBs of both sliders incorporate a 8-pin male Picoflex® connector (header). Each of these standalone sliders ships with the female 8-pin Picoflex® connector (receptacle) that mates with the connector (header) on the board. Please see the Pin Diagram tab for details.

Specifications | ||
---|---|---|
Item # | ELLC2 | |
DC Voltage Input to Controller | 4.5 to 5.5 V | |
Typical Current Consumption Per Module | Movement | 800 mA |
Standby | 50 mA | |
Operating Temperature Range | 15 to 40 °C | |
Ribbon Cable Length (1 Included) | 250 mm (9.84") | |
Maximum Supported Ribbon Cable Length |
500 mm (19.68") | |
Dimensions (Interface Only) | 66.0 mm x 32.0 mm x 12.5 mm (2.60" x 1.26" x 0.49") |
|
Weight (Interface Only) | 10.8 g (0.022 lbs) |
- Convert Any Single ELL Device into a Kit by Adding the Following:
- Handheld Controller
- USB Micro B Cable
- Picoflex®1 Cable
- 5 V Power Supply with Regional Adapter (US, UK, AU, or EU)
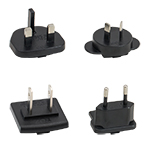
Click for Details
Region-Specific Adapters for the ELLC2 Power Adapter
Thorlabs' ELLC2 Accessory Upgrade Pack is designed to include all of the items necessary to convert any single ELL slider, stage, or mount into an ELL kit2. The included handheld controller features three buttons to control the position of a connected ELL stage and the USB port enables direct connection to a PC via the included USB Micro B cable. A 0.25 m Picoflex® cable with 8 loaded circuits that connects the handheld controller to the ELL device and a 5 V power supply with a regional adapter (US, UK, AU, or EU) are also included with the kit.
- Note: Picoflex® is a registered trandemark of Molex Incorporated.
- Mounting brackets for the ELL17(/M), ELL18(/M), and ELL20(/M) can be ordered by contacting Tech Support.

Specifications | ||
---|---|---|
Item # | ELLB | |
Voltage Rating | 4.5 to 5.5 V | |
Typical Current Consumption Per Module | Movement | 800 mA |
Standby | 50 mA | |
Maximum Board Current | 4.0 A | |
Operating Temperature Range | 15 to 40 °C | |
Ribbon Cable Length (4 Included) | 250 mm | |
Maximum Supported Ribbon Cable Length |
500 mm | |
Dimensions | 65.0 mm x 32.0 mm x 12.5 mm (2.56" x 1.26" x 0.49") |
|
Weight | 11 g (0.02 lbs) |
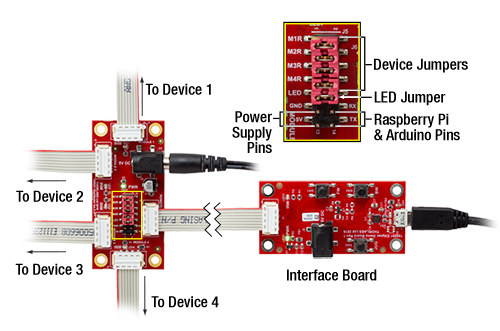
Click to Enlarge
A single bus distributor can be used to control up to four Elliptec devices. The bus can be connected to a PC using the interface board provided with the bundles sold above. Note that the bus is then controlled by the Elliptec software and that the buttons on the interface board are disabled.
- Control and Power up to Four Elliptec® Devices with One Bus
- Daisy Chain Bus Boards to Control up to 16 Elliptec Devices
- Controlled Remotely Using Elliptec System Software (See Software Tab Above)
- Connect to PC Using USB Interface Board Included with Elliptec Bundles
- Five Jumpers and Four 8-Conductor 28 AWG Ribbon Cables Included
- Compatible with Raspberry Pi® and Arduino® Boards
The ELLB Bus Distributor connects up to four Elliptec® devices. Connected devices can be controlled with or without the interface board included with the above bundles. When using the interface board, each connected device is controlled remotely by a PC running the Elliptec software package. The interface board connects to the bus's input port labeled REMOTE; once connected, the interface board's buttons are disabled. For control without using the interface board, see the Pin Diagrams tab for custom connections.
Multiple ELLB Bus Distributors can be daisy chained to control and power up to 16 Elliptec devices; simply connect one of the four MODULE outputs to the second board's REMOTE input. Indicator LEDs are provided to show which device is active. The communications protocol manual describes how to use the software to individually address each connected device. A link to download the software and accompanying documentation can be found in the Software tab.
The bus includes a Ø6.3 mm power connector that supports a 5 V supply with a maximum current of 4 A. As more devices are connected, simultaneous control of the units will require more current to be provided by the power supply; please see the Specs tab for the amount of current drawn by each Ellitpec device. A 5 V, 1 A power supply is included with the above ELL9 and ELL12 bundles. Depending on the current draw of the Elliptec devices connected, this supply provides enough current to power two devices simultaneously.
Fourteen control pins, detailed in the image to the right, are included for additional functionality. Four pairs of pins are each shorted with a jumper that, when in place, enables the Elliptec software to receive feedback from connected Elliptec devices. The pair of pins labeled LED is shorted with a jumper that, when removed, will disable the indicator LEDs. The 5V and GND allow an optional, user-provided 5 V, 2 A power supply to be used in place of a source connected to the Ø6.3 mm power connector. The RX and TX pins can be used to control the bus with a Raspberry Pi® or Arduino® board, respectively, instead of the Elliptec interface board.
The board is mounted using the Ø3.5 mm through holes provided in each corner. Four 8-conductor, 28 AWG ribbon cables are included.
Compatible Elliptec Devices | |||||
---|---|---|---|---|---|
![]() |
![]() |
![]() |
![]() |
![]() |
![]() |
Multi-Position Sliders | 28 mm Linear Stage | 60 mm Linear Stage | Rotation Stage | Rotation Mount | Motorized Iris |

Using ELLA1 post mount adapters allow sliders to be placed one behind the other while minimizing the space between them.
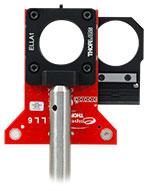
Click to Enlarge
The ELLA1 mounts to the back of the slider's PCB using the four 4-40 threaded holes, also compatible with 30 mm cage system components.
- Mounts Directly to Slider PCB
- Front Clearance Slot Accommodates Protrusions on Back of PCB
- Four Counterbores for Use with 4-40 Threaded Screws
- One Counterbore for Use with 8-32 (M4) Threaded Screws
- SM1 (Ø1.035-40) Internal Thread
The ELLA1 Post Mount Adapter securely fastens to the back of the multi-position slider PCB using the four included 4-40 screws. The slider can then be mounted to a Ø1/2" post using the counterbore at the base of the adapter and an 8-32 (M4) screw (not included). A lens tube or other component can be mated to the adapter using the internally SM1-threaded (1.035"-40) bore. The four counterbores can also be used to connect the ELLA1 to a 30 mm cage system via Ø6 mm cage rods.
With overall dimensions of 40.0 mm x 44.0 mm x 14.0 mm and a design that positions the mounting post close to the back of the slider's PCB, the adapter is especially recommended for applications that require placing sliders one closely behind the other. The geometry of the adapter allows the optics mounted on one slider to be positioned above the post used to mount the slider directly in front. These adapters are also convenient single-component mounting solutions for general applications.