Kinesis® 30 mm XY Stage with Integrated Controller, Brushed DC Servo Motors
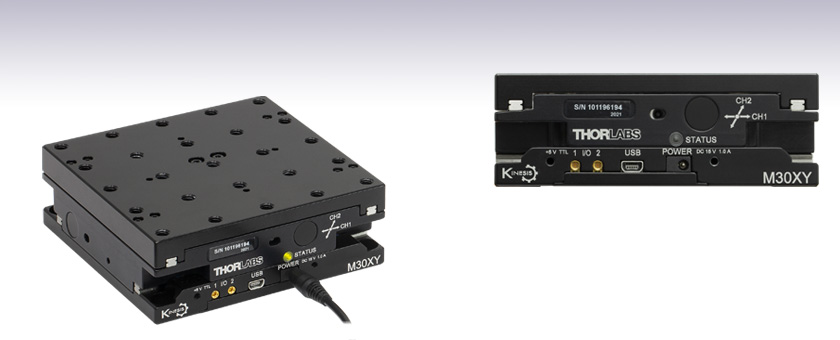
- 30 mm Travel Along X and Y Axes at Speeds Up to 2.4 mm/s
- Integrated DC Servo Motors and Control Electronics
- Bidirectional Repeatability of ±1.0 µm
M30XY
30 mm XY Translation Stage
The unit features connections for PC control and external triggering.

Please Wait
Key Specificationsa | |
---|---|
Travel | 30 mm x 30 mm (1.18" x 1.18") |
Load (Max) | Horizontal: 5.0 kg (11.02 lbs) Vertical: 2.0 kg (4.41 lbs) |
Speed (Max) | 2.4 mm/s (All Loads) |
Bidirectional Repeatability |
±1.0 µm |
Pitch Angular Deviation | ±100 µrad |
Yaw Angular Deviation | ±50 µrad |
Dimensions | 115 mm x 115 mm x 40 mm (4.53" x 4.53" x 1.57") |
Features
- Motorized Precision XY Translation Stage
- Remote PC Control via USB
- External Bidirectional Triggering via I/O Ports (5 V TTL)
- Smooth, DC-Servo-Driven Linear Motion
- Full Kinesis® Software Control Suite Included
- Large Mounting Platform with 1/4"-20 (M6) Taps
- Location-Specific Power Supply Included
- Vertical Mounting for XZ Travel Using M30A2(/M) Bracket (Sold Separately)
The M30XY(/M) Motorized XY Translation Stage is a DC-servo-driven, 2-axis linear stage with integrated drive electronics. This stage provides precise, stable linear adjustment over the full translation range. The stage motor is capable of moving loads up to 5.0 kg on a large 115 mm x 115 mm mounting platform with minimal pitch and yaw deviation. Recirculating bearings and an optical linear encoder ensure accurate positioning with high repeatability. See the Specs tab for complete specifications.
The top plate has twenty-five 1/4"-20 (M6 x 1.0) taps on 1" (25.0 mm) centers for mounting optomechanical subassemblies. The base of each unit has four through holes that accept 1/4"-20 or M6 screws for mounting to imperial or metric breadboards, respectively. The unit is supplied with a region-specific power supply with an input of 100 to 240 VAC. The connectors on side of the unit can be secured in place using the M30A1 clamp to avoid accidental disconnection, especially useful when mounted vertically or on top of another stage or assembly. Note that the power supply unit (PSU) should be connected to the stage before connecting the PSU to a power outlet. A USB cable for controlling the stage via PC is also included.
A USB port on the side of the stage allows it to be connected to a PC and controlled using our Kinesis® software suite. This software package features new .NET controls that can be used by 3rd party developers working in the latest C#, Visual Basic, LabVIEW, or any .NET compatible languages to create custom applications. Parameter settings can be adjusted on the PC and stored in non-volatile memory within the unit itself. When the unit is next powered up, these settings are applied automatically. Please see the Kinesis Software and Kinesis Tutorials tabs for more details. External bidirectional triggering is possible using the two I/O ports on the unit.
Specificationsa | |
---|---|
Travel | 30 mm x 30 mm (1.18" x 1.18") |
Max Speed | 2.4 mm/s |
Acceleration | 5.0 mm/s 2 |
Bidirectional Repeatability | ±1.0 µm |
Backlasha | N/A |
Min Repeatable Incremental Movement | 2.5 µm |
Home Location Accuracy | ±1.75 µm |
Max Load | Horizontal Mounting: 5.0 kg (11.02 lbs) Vertical Mounting: 2.0 kg (4.41 lbs) |
Accuracy | 8 µm |
Pitch Angular Deviation | ±100 µrad |
Yaw Angular Deviation | ±50 µrad |
Horizontal Straightness | ±2.5 µm |
Vertical Straightness | ±2.5 µm |
Limit Switches | X and Y as Standard |
Bearing Type | High Rigidity Recirculating Precision Linear Bearing |
Motor Type | Brushed DC Motor |
Motor Output | |
Motor Drive Voltage | ±15 V |
Motor Drive Current (per Axis, Loaded)b |
<100 mA (Continuous) <150 mA (Vertical Movement) |
Control Algorithm | Digital PID Filter (16 Bit) |
Position Counter | 32 Bit |
Velocity Profie | Trapezoidal |
Input Power Requirements | |
Voltage | 15 V Regulated DC |
Current | 500 mA (Peak) |
General Data | |
Dimensions at Mid Travel (W x D x H) |
115 mm x 115 mm x 40 mm (4.53" x 4.53" x 1.57") |
Weight | 1.2 kg (2.65 lbs) |
Computer Connection
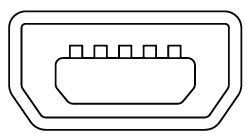
USB 2.0 Mini-AB Connector
I/O 1MMCX Female |
I/O 2MMCX Female |
![]() |
![]() |
+5 V TTL | +5 V TTL |
These connectors can be independently configured for use with external trigger input or output signal (5 V TTL levels). | |
In input mode, a voltage level less than 1.5 V is recognized as logic Low, and a level greater than 3.5 V is registered as logic High. As the input contains a weak pull-up, the state of the input with nothing connected will default to a logic High. The weak pull-up feature allows a passive device, such as a mechanical switch, to be connected directly to the input. | |
In output mode, the port provides a push-pull drive of 5 V with a maximum current of 8 mA. |
Power Supply
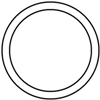
3.15 mm Jack Connector
Each M30XY(/M) stage includes the following components:
- 2-Axis Translation Stage
- Two MMCX Male to BNC Male Cables, Each 1.8 m Long, 50 Ω
- USB2.0 A to Mini-B Cable, 1.5 m, Black
- 15 VDC Power Supply with Region-Specific Plug
Applications
The M30XY(/M) linear translation stage features a top plate with 1/4"-20 (M6 x 1.0) taps on 1" (25.0 mm) centers and four through holes that accept 1/4"-20 or M6 screws, which provide compatibility with several other Thorlabs translation stages. By constructing assemblies with additional axes of translation, this linear translation stage can be used in a variety of applications including inspection, laser alignment, fiber launch alignment, and microscopy. Example assemblies are shown in the table below.
M30XY(/M) Example Assemblies | |||
---|---|---|---|
Item #s | M30X(/M) M30XY(/M) M30A1 (Qty. 2) M30A2(/M) |
M30XY(/M) M30A1 KVS30(/M) |
M30XY(/M) MAX311D(/M) |
Image (Click to Enlarge) |
![]() |
![]() |
![]() |
Axis Configuration | XYZ | XYZ | XY and XYZ |
Integrated Controllers | ![]() |
![]() |
-a |
Fully Automated | ![]() |
![]() |
![]() |
Motor Type | DC Servo | DC Servo | DC Servo Closed-Loop Piezo |
Vertical Load | 2 kg | 5 kg | 1 kg |
Travel | 30 mm (X, Y, and Z) | 30 mm (X, Y, and Z) | Servo: 30 mm (X and Y) |
Piezo: 20 µm +0.2 µm / -0.0µm (X, Y, and Z) Coarse Differential: 4 mm (X, Y, and Z) Fine Differential: 0.3 mm (X, Y, and Z) |
|||
Repeatability | ±1 µm (X, Y, and Z) | ±1 µm (X and Y) ± 0.12 µm (Z) |
Servo: ±1 µm Piezo: ±25 nm |
Accuracy | 8 µm (X, Y, and Z) | 8 µm (X and Y) 0.9 µm (Z) |
- |
Velocity | 2.4 mm/s (X, Y, and Z) | 2.4 mm/s (X and Y) 8 mm/s (Z) |
- |
Software
Kinesis Version 1.14.50
The Kinesis Software Package, which includes a GUI for control of Thorlabs' Kinesis system controllers.
Also Available:
- Communications Protocol
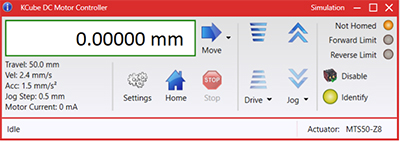
Kinesis GUI Screen
Thorlabs offers the Kinesis® software package to drive our wide range of motion controllers. The software can be used to control devices in the Kinesis family, which covers a wide variety of motion controllers ranging from small, low-powered, single-channel drivers (such as the K-Cubes™) to high-power, multi-channel benchtop units and modular 19" rack nanopositioning systems (the MMR60x Rack System).
The Kinesis Software features .NET controls which can be used by 3rd party developers working in the latest C#, Visual Basic, LabVIEW™, or any .NET compatible languages to create custom applications. Low-level DLL libraries are included for applications not expected to use the .NET framework and APIs are included with each install. A Central Sequence Manager supports integration and synchronization of all Thorlabs motion control hardware.
By providing this common software platform, Thorlabs has ensured that users can mix and match any of our motion control devices in a single application, while only having to learn a single set of software tools. In this way, it is perfectly feasible to combine any of the controllers from single-axis to multi-axis systems and control all from a single, PC-based unified software interface.
The software package allows two methods of usage: graphical user interface (GUI) utilities for direct interaction with and control of the controllers 'out of the box', and a set of programming interfaces that allow custom-integrated positioning and alignment solutions to be easily programmed in the development language of choice.
Legacy Software
Select products are still capable of running the legacy APT™ software package. Information on software compatibility can be found in the product documentation (), and additional details about the APT software can be found here.
Thorlabs' Kinesis® software features new .NET controls which can be used by third-party developers working in the latest C#, Visual Basic, LabVIEW™, or any .NET compatible languages to create custom applications.
C#
This programming language is designed to allow multiple programming paradigms, or languages, to be used, thus allowing for complex problems to be solved in an easy or efficient manner. It encompasses typing, imperative, declarative, functional, generic, object-oriented, and component-oriented programming. By providing functionality with this common software platform, Thorlabs has ensured that users can easily mix and match any of the Kinesis controllers in a single application, while only having to learn a single set of software tools. In this way, it is perfectly feasible to combine any of the controllers from the low-powered, single-axis to the high-powered, multi-axis systems and control all from a single, PC-based unified software interface.
The Kinesis System Software allows two methods of usage: graphical user interface (GUI) utilities for direct interaction and control of the controllers 'out of the box', and a set of programming interfaces that allow custom-integrated positioning and alignment solutions to be easily programmed in the development language of choice.
For a collection of example projects that can be compiled and run to demonstrate the different ways in which developers can build on the Kinesis motion control libraries, click on the links below. Please note that a separate integrated development environment (IDE) (e.g., Microsoft Visual Studio) will be required to execute the Quick Start examples. The C# example projects can be executed using the included .NET controls in the Kinesis software package (see the Kinesis Software tab for details).
![]() |
Click Here for the Kinesis with C# Quick Start Guide Click Here for C# Example Projects Click Here for Quick Start Device Control Examples |
![]() |
LabVIEW
LabVIEW can be used to communicate with any Kinesis- or APT-based controller via .NET controls. In LabVIEW, you build a user interface, known as a front panel, with a set of tools and objects and then add code using graphical representations of functions to control the front panel objects. The LabVIEW tutorial, provided below, provides some information on using the .NET controls to create control GUIs for Kinesis- and APT-driven devices within LabVIEW. It includes an overview with basic information about using controllers in LabVIEW and explains the setup procedure that needs to be completed before using a LabVIEW GUI to operate a device.
![]() |
Click Here to View the LabVIEW Guide Click Here to View the Kinesis with LabVIEW Overview Page |
![]() |
Motorized Linear Translation Stages
Thorlabs' motorized linear translation stages are offered in a range of maximum travel distances, from a stage with 20 µm of piezo translation to our 600 mm direct drive stage. Many of these stages can be assembled in multi-axis configurations, providing XY or XYZ translation. For fiber coupling applications, please see our multi-axis stages, which offer finer adjustment than our standard motorized translation stages. In addition to motorized linear translation stages, we offer motorized rotation stages and goniometers. We also offer manual translation stages.
Piezo Stages
These stages incorporate piezoelectric elements in a variety of drive mechanisms. ORIC® stages incorporate piezo inertia drives that use "stick-slip" friction properties to obtain extended travel ranges. Our Nanoflex™ translation stages use standard piezo chips along with manual actuators. Elliptec® stages use resonant piezo motors to push and pull the moving platform through resonant elliptical motion. Our LPS710E z-axis stage features a mechanically amplified piezo design and includes a matched controller.
Piezoelectric Stages | ||||
---|---|---|---|---|
Product Family | ORIC® PDXZ1 Closed-Loop 4.5 mm Vertical Stage |
ORIC® PD2 Open-Loop 5 mm Stage |
ORIC® PDX2 Closed-Loop 5 mm Stage |
|
Click Photo to Enlarge |
![]() |
![]() |
![]() |
|
Travel | 4.5 mm | 5 mm | ||
Speed | 1 mm/s (Typ.)a | 10 mm/s (Typ. Max)b | 8 mm/s (Typ.)c | |
Drive Type | Piezoelectric Inertia Drive | |||
Possible Axis Configurations | Z | X, XY, XYZ | ||
Mounting Surface Size |
45.0 mm x 42.0 mm | 13 mm x 13 mm | ||
Additional Details |
Piezoelectric Stages | ||||||
---|---|---|---|---|---|---|
Product Family | ORIC® PD1 Open-Loop 20 mm Stage |
ORIC® PD1D Open-Loop 20 mm Monolithic XY Stage |
ORIC® PDX1 Closed-Loop 20 mm Stage |
ORIC® PDX1A Closed-Loop 20 mm Stage Low-Profile |
ORIC® PD3 Open-Loop 50 mm Stage |
|
Click Photo to Enlarge |
![]() |
![]() |
![]() |
![]() |
![]() |
|
Travel | 20 mm | 50 mm | ||||
Speed | 3 mm/s (Typ. Max)a | 20 mm/s (Typ. Max)c | 10 mm/s (Typ.)b | 10 mm/sd | ||
Drive Type | Piezoelectric Inertia Drive | |||||
Possible Axis Configurations | X, XY, XYZ | XY, XYZ | X, XY, XYZ | X, XY, XYZ | X, XY, XYZ | |
Mounting Surface Size |
30 mm x 30 mm | 80 mm x 30 mm | ||||
Additional Details |
Piezoelectric Stages | ||||||
---|---|---|---|---|---|---|
Product Family | Nanoflex™ 20 µm Stage with 5 mm Actuator |
Nanoflex™ 25 µm Stage with 1.5 mm Actuator |
Elliptec® 28 mm Stage | Elliptec® 60 mm Stage | LPS710E 1.1 mm Vertical Stage | |
Click Photo to Enlarge |
![]() |
![]() |
![]() |
![]() |
![]() |
|
Travel | 20 µm + 5 mm Manual | 25 µm + 1.5 mm Manual | 28 mm | 60.0 mm | 1.1 mm | |
Maximum Velocity | - | 180 mm/s | 90 mm/s | - | ||
Drive Type | Piezo with Manual Actuator | Resonant Piezoelectric Motor | Amplified Piezo | |||
Possible Axis Configurations | X, XY, XYZ | X | Z | |||
Mounting Surface Size | 75 mm x 75 mm | 30 mm x 30 mm | 15 mm x 15 mm | 21 mm x 21 mm | ||
Additional Details |
Stepper Motor Stages
These translation stages feature removable or integrated stepper motors and long travel ranges up to 300 mm. Many of these stages either have integrated multi-axis capability (PLSXY) or can be assembled into multi-axis configurations (PLSX, LNR Series, NRT Series, and LTS Series stages). The MLJ150 stage also offers high load capacity vertical translation.
Stepper Motor Stages | |||||
---|---|---|---|---|---|
Product Family | PLSX with and without PLST(/M) Top Plate 1" Stage |
PLSXY with and without PLST(/M) Top Plate 1" Stage |
LNR Series 25 mm Stage |
LNR Series 50 mm Stage |
|
Click Photo to Enlarge |
![]() |
![]() |
![]() |
![]() |
|
Travel | 1" | 25 mm | 50 mm | ||
Maximum Velocity | 7.0 mm/s | 2.0 mm/s | 50 mm/s | ||
Possible Axis Configurations |
X, XY | X, XY, XYZ | X, XY, XYZ | ||
Mounting Surface Size |
3" x 3" | 60 mm x 60 mm | 100 mm x 100 mm | ||
Additional Details |
Stepper Motor Stages | ||||||
---|---|---|---|---|---|---|
Product Family | NRT Series 100 mm Stage |
NRT Series 150 mm Stage |
LTS Series 150 mm Stage |
LTS Series 300 mm Stage |
MLJ250 50 mm Vertical Stage |
|
Click Photo to Enlarge |
![]() |
![]() |
![]() |
![]() |
![]() |
|
Travel | 100 mm | 150 mm | 150 mm | 300 mm | 50 mm | |
Maximum Velocity | 30 mm/s | 50 mm/s | 3.0 mm/s | |||
Possible Axis Configurations |
X, XY, XYZ | X, XY, XYZ | Z | |||
Mounting Surface Size |
84 mm x 84 mm | 100 mm x 90 mm | 148 mm x 131 mm | |||
Additional Details |
DC Servo Motor Stages
Thorlabs offers linear translation stages with removable or integrated DC servo motors. These stages feature low profiles and many can be assembled in multi-axis configurations.
DC Servo Motor Stages | ||||
---|---|---|---|---|
Product Family | MT Series 12 mm Stages |
PT Series 25 mm Stages |
MTS Series 25 mm Stage |
MTS Series 50 mm Stage |
Click Photo to Enlarge |
![]() |
![]() |
![]() |
![]() |
Travel | 12 mm | 25 mm | 25 mm | 50 mm |
Maximum Velocity | 2.6 mm/s | 2.4 mm/s | ||
Possible Axis Configurations | X, XY, XYZ | X, XY, XYZ | ||
Mounting Surface Size |
61 mm x 61 mm | 101.6 mm x 76.2 mm | 43 mm x 43 mm | |
Additional Details |
DC Servo Motor Stages | ||||
---|---|---|---|---|
Product Family | M30 Series 30 mm Stage |
M30 Series 30 mm Monolithic XY Stage |
M150 Series 150 mm XY Stage |
KVS30 30 mm Vertical Stage |
Click Photo to Enlarge |
![]() |
![]() |
![]() |
![]() |
Travel | 30 mm | 150 mm | 30 mm | |
Maximum Velocity | 2.4 mm/s | X-Axis: 170 mm/s Y-Axis: 230 mm/s |
8.0 mm/s | |
Possible Axis Configurations | X, Z | XY, XZ | XY | Z |
Mounting Surface Size |
115 mm x 115 mm | 272.4 mm x 272.4 mm | 116.2 mm x 116.2 mm | |
Additional Details |
Direct Drive Stages
These low-profile stages feature integrated brushless DC servo motors for high speed translation with zero backlash. When no power is applied, the platforms of these stages have very little inertia and are virtually free running. Hence these stages may not be suitable for applications where the stage's platform needs to remain in a set position when the power is off. We do not recommend mounting these stages vertically.
Direct Drive Stages | |||||
---|---|---|---|---|---|
Product Family | DDS Series 50 mm Stage |
DDS Series 100 mm Stage |
DDS Series 220 mm Stage |
DDS Series 300 mm Stage |
DDS Series 600 mm Stage |
Click Photo to Enlarge |
![]() |
![]() |
![]() |
![]() |
![]() |
Travel | 50 mm | 100 mm | 220 mm | 300 mm | 600 mm |
Maximum Velocity | 500 mm/s | 300 mm/s | 400 mm/s | 400 mm/s | |
Possible Axis Configurations | X, XY | X, XY | X | X | |
Mounting Surface Size | 60 mm x 52 mm | 88 mm x 88 mm | 120 mm x 120 mm | ||
Additional Details |
Posted Comments: | |
user
 (posted 2024-04-26 11:22:30.78) I have a question regarding the position accuracy of the stage model M30XY/M.
Let me first describe use-case scenario. I am performing a typical knife-edge measurement to profile a laser beam diameter. In more detail, the knife is mounted on the M30XY/M stage. The stage moves the knife in small, discrete steps in one direction across the laser beam. For each knife position, I am recording the transmitted laser power and the stage position as displayed in the kinesis software/obtained via the API.
I was wondering how accurate the displayed knife-positions are. On the spec sheet, I see a value for accuracy of 8µm. Is this the correct tolerance or is the bidirectional repeatability more relevant for my application?
Is the specified accuracy tolerance a symmetric (i.e., "plus-minus")-tolerance? E.g., when the kinesis software displays the position "2.000 mm", the actual position might be "1.992 mm" up to "2.008 mm"?
Thank you very much. do'neill
 (posted 2024-04-29 07:31:12.0) Thank you for your comment. Firstly the accuracy is symmetric and therefore ±8µm. This is, as you said, how close the position is to the "true" position, e.g. 1.992mm-2.008mm in your example. Where as bi-directional repeatability is how close it returns to the same value each time it is commanded to move to the same position.
I will reach out to you directly to discus your application in more detail. user
 (posted 2024-02-01 13:29:32.017) Hello,
I am currently trying to control M30XY motor using python and it seems to work fine. But it keeps on stopping randomly and give the following error.
Device is not enabled
at Thorlabs.MotionControl.GenericMotorCLI.AdvancedMotor.GenericAdvancedMotorCLI.VerifyDeviceMovement(Int32 functionDepth, VerifyMovementFlags flags)
at Thorlabs.MotionControl.GenericMotorCLI.AdvancedMotor.GenericAdvancedMotorCLI.MoveTo(Decimal position, Int32 waitTimeout)
Thanks, cstroud
 (posted 2024-02-12 08:06:40.0) Thanks for reaching out. I will contact you directly to help troubleshoot your script. Anway Pimpalkar
 (posted 2023-12-15 16:50:37.453) I'm interested in using Python or MATLAB to control an M30XY stage. Could you please help me understand how that can be done? Thanks. do'neill
 (posted 2024-01-02 11:55:24.0) Thank you for your enquiry. A minimum working example for controlling the M30XY using Python can be found on out GitHub at https://github.com/Thorlabs/Motion_Control_Examples/blob/main/Python/Benchtop/M30X(Y)/m30xy_pythonnet.py. user
 (posted 2022-05-20 13:00:38.91) Hi Thorlabs Team, I have found example code to control the KDC101 with python using the ctypes library, but was wondering if the example code DJayasuriya sent Jisoo Kyoung on 2021-10-29 08:40:58 was specifically for the M30XY? If so, could you please send it to me via email? Thanks DJayasuriya
 (posted 2022-05-24 04:40:03.0) Thank you for your inquiry. We will get in touch with you directly to helpd with your request. G Beach
 (posted 2022-05-17 16:13:00.657) Hello! I have been trying to control the M30XY stage using python as well, but am having trouble. Would you be able to share the example code with me in the text of an email? Thank you for your help! cwright
 (posted 2022-05-18 08:31:03.0) Response from Charles at Thorlabs: Thank you for your query. We will reach out to you to discuss programming this device in Python. user
 (posted 2022-05-10 18:37:45.43) Hello, I'm also interested in using Python to control an M30XY stage. Could I please be sent the example code DJayasuriya sent Jisoo Kyoung on 2021-10-29 08:40:58? Thank you! DJayasuriya
 (posted 2022-05-11 05:49:05.0) Thank you for your inquiry, of course, I've have got in touch with you directly. Anandh Balakrishnan
 (posted 2022-03-11 17:22:10.067) Hi there-
I have purchased this system. Just a quick clarification-
Since the control algorithm is built in, do I really need to connect the TTL ports to an external trigger? Can I not just use Kinesis SW via the USB to control the stage bidirectionally?
Are the triggers to provide an external event driven control?
Best
Anandh DJayasuriya
 (posted 2022-03-25 10:24:13.0) Thank you for your inquiry. Yes you are able to use Kinesis with out the TTL ports being connected. We have got in touch with you directly to discuss your application. Juwon Oh
 (posted 2022-02-03 14:11:51.903) Dear whom to concern it
Hi, this is Juwon.
Now, I am trying to control your M30XY/M stage with Labview program.
I tried to NET control with KCubeDCServoControl in Thorlabs.MotionControl.Controls.dll. (I also tried it with TCubeDCServoControl, BenchtopDCServoControl and BenchtopBrushlessControl).
But all is failed with error message "No Suitable Devices Found".
Can you give me some advice to use this stage with Labview program?
Best wishes,
Juwon cwright
 (posted 2022-02-03 05:44:36.0) Response from Charles at Thorlabs: Thank you for your query. BenchtopDCServoControl is the correct control. Usually this issue could be caused by having the device already open in another piece of software. Alternatively there may be a missing feature in your VI. We will reach out to you to troubleshoot your VI. Jisoo Kyoung
 (posted 2021-10-27 21:08:23.77) Dear Thorlabs,
Hi, I am interested in your M30XY/M.
I would like to control the M30XY/M by Python code.
Is it possible to use Python instead of Kinesis Software?
If you have any example code, please send me.
Thanks. DJayasuriya
 (posted 2021-10-29 08:40:58.0) Thank you for your inquiery, Yes we do provide the DLLs files when Kinesis or APT software is installed. Using the DLLs provided you would be able to use Python to write your code. I will get in touch with you directly with the example code. |

- 30 mm Translation in X and Y
- ±1.0 µm Bidirectional Repeatability
- 2.5 µm Minimum Incremental Movement
- 40 mm Deck Height
- Control Remotely by PC via USB
- External Bidirectional Triggering via I/O Ports (5 V TTL)
This 2-axis motorized translation stage provides 30 mm of precise, stable adjustment per axis with smooth, repeatable motion. The large 115 mm x 115 mm platform is capable of moving loads up to 5.0 kg at speeds up to 2.4 mm/s. Note that the M30XY(/M) stage is monolithic and cannot be disassembled into two single-axis stages.
The USB connector allows PC control using our Kinesis® software control suite. Two I/O ports enable external bidirectional triggering (5 V TTL). Two CA3272 cables for these ports are included with each stage. Replacement cables are also available below. A power supply with a region-specific adapter plug is included with the stage.

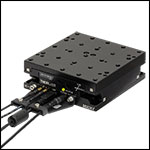
Click to Enlarge
M30XY Stage Shown with M30A1 Cable Retention Clamp (Each Sold Separately)
- M30A2(/M) Vertical Mounting Bracket for XZ or XYZ Applications
- M30A1 Cable Retention Clamp
The M30A2 and M30A2/M Right-Angle Brackets are designed to vertically mount M30XY and M30XY/M stages, respectively. The base of each stage can be secured to the mounting bracket using four 1/4"-20 (M6 x 1.0) cap screws in the mounting holes near the corners. Four Ø3 mm dowel pin holes are located on each face for precise alignment. The XY stage must be mounted on the right-angle bracket with the connectors facing up. We recommend using the M30A1 cable clamp when mounting vertically to support the connected cables. Note that when the M30XY(/M) stage is mounted for vertical translation, the load capacity is reduced to 2.0 kg (4.41 lbs).
The M30A1 cable clamp offers additional support for and retention of cables connected to the M30XY(/M) stage. We strongly recommend the use of the clamp when mounting the stage vertically or on top of another stage or assembly.

- Cables for Trigger Ports on M30XY(/M) Translation Stage
- MMCX Male Connector to BNC or SMA Male Connector
- DC - 6 GHz Frequency Range
- 50 Ω Normal Impedance
- 170 V Max Operating Voltage
These cables enable external triggering via the I/O ports on the M30XY(/M) stage. The CA3339 (1 m long) and CA3272 (1.8 m long) cables each feature a male BNC termination while the CA3439 has a male SMA termination.