ORIC® 4.5 mm Vertical Translation Stage with Piezoelectric Inertia Drive
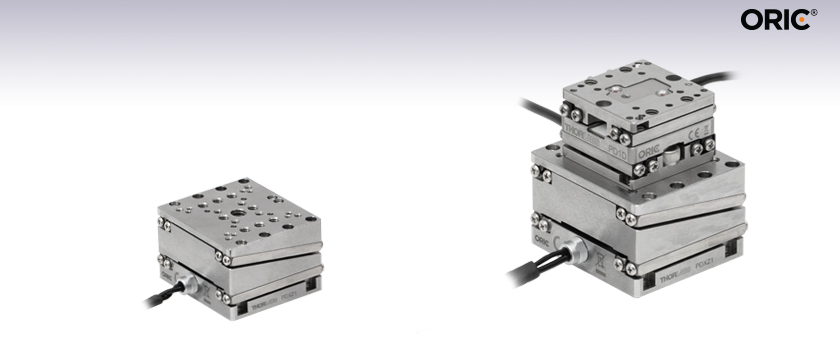
- 4.5 mm Vertical Travel Stage with Open- or Closed-Loop Positioning
- Versatile Design for Easy Configuration with Other Setups
- 1 kg Vertical Load Capacity
PDXZ1
4.5 mm Vertical Travel
Piezo Inertia Stage
with Optical Encoder
Application Idea
PD1D 20 mm Travel XY Stage and
PDXZ1 Vertical Stage in XYZ Configuration
U.S. Patent 11,606,045

Please Wait
ORIC® Piezo Inertia Stage Selection Guide |
---|
4.5 mm Vertical Translation Stage |
5 mm Linear Translation Stages |
20 mm Linear Translation Stages |
50 mm Linear Translation Stage |
Rotation Stages |
Vacuum-Compatible Stages |
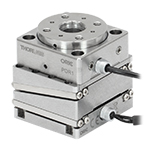
Click for Details
A Z + R translation stage created by mounting a PDR1(/M) rotation stage on a PDXZ1(/M) vertical stage.
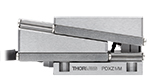
Click to Enlarge
Side view of the PDXZ1/M stage at its bottom extended range.
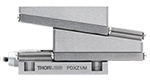
Click to Enlarge
Side view of the PDXZ1/M stage at its top extended range.
Features
- Compact Stainless Steel Stage with Piezo Inertia Drive
- Ideal for OEMs and Set-and-Hold Applications that Require Relative Positioning with High Resolution
- Accessories Sold Separately Below
- Universal Mounting Adapter Provides a Flat Surface for Mounting the Stage
- Adapter Plates Provide Alternative Mounting Hole Patterns
- Piezo Inertia Stage Controller (Required)
Thorlabs' PDXZ1(/M) Series ORIC® Piezoelectric Inertia Drive Stage (U.S. Patent 11,606,045) provides fast and stable piezo-controlled vertical motion in a compact package with no backlash. The PDXZ1(/M) stage provides open- and closed-loop operation with an integrated optical encoder. The piezo inertia drive is self-locking when the stage is at rest and no power is supplied to the piezo, making these stages ideal for set-and-hold applications that require nanometer resolution and long-term alignment stability. The stage can drive a load of 1 kg (2.2 lbs) using continuous long-term stepping or periodic positioning modes with a typical stepping speed of 1 mm/s, or be used in a hold mode with 20 N of clamping/holding force.
Load Mounting Options
The load can be secured to the stage's top platform using a variety of mounting features including 2-56 (M2 x 0.4), 8-32 (M4 x 0.7), and 1/4"-20 (M6 x 1.0) threaded holes. The PDXZ1 imperial and PDXZ1/M metric stages both feature 4-40 and M3 x 0.5 taps for additional mounting options (See the Specs tab for more details). The bottom plate of the PDXZ1(/M) stage features four #2 (M2) counterbores and four 2-56 (M2 x 0.4) taps for mounting. Alternatively, the PD1T(/M) and PD1U(/M) adapter plates (sold separately) provide additional mounting hole patterns for the top plate of the stage. The load can also be aligned using the array of Ø2 mm, 1.5 mm deep dowel pin holes; see the drawings below for details. Thorlabs also offers replacement dowel pins in packs of 20 below. Ensure that the maximum insertion depth of these holes is not exceeded or else the stage may be damaged. For more information, please refer to the Specs tab or the support documents accessible through the red Support Docs icons )
Stage Mounting Options
The mounting counterbores are accessible when the moving plate is translated to the ends of the travel range. The stage can be mounted using the two, included, 2-56 (M2 x 0.4) screws on the corners with 0.35 N·m recommended torque. We offer the TD75 torque driver for tightening to a specific torque value.
The stage should be mounted on an even surface with recommended flatness ≤5 μm. If the stage is mounted on a surface with >5 µm flatness (as with most breadboards and optical tables), the mounting torque may need to be decreased in order for the velocity variation and pitch/roll of the stage to meet specifications. If needed, PD1B3(/M) mounting adapters provide a mounting surface with precise flatness to avoid warping the stage when mounting it to a table surface.
Once mounted to the PD1B3(/M) adapter, the adapter can then be used to mount the stage to other stages such as the LX10(/M) 25 mm translation stage, an M30XY(/M) 30 mm motorized XY translation stage, and other manual or motorized stages.
Compatibility with Other ORIC Stages
The PDXZ1(/M) stage can be combined with an ORIC rotation stage for applications that require vertical translation and rotation, an example of which is shown to the right. Additionally, many of Thorlabs' ORIC linear stages such as the PD1(/M), PD1D(/M), PDX1(/M), or PDX1A(/M) stages can be mounted using mounting holes on the top of the stage. Please see the Specs tab for more details on the compatibility with other ORIC stages and products.
Required Controller
One of our PDXC or PDXC2 piezo inertia controllers is required to operate these stages. Note that the piezo inertia drives cannot be driven using a standard piezo controller.
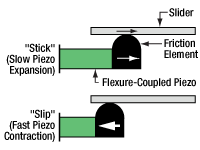
Click to Enlarge
Simplified Illustration Showing the Operation of the Piezo Inertia Drive
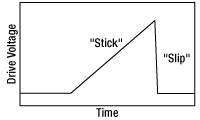
The "stick-slip" cycle consists of a slow piezo expansion and a fast piezo contraction.
Piezoelectric Inertia "Stick-Slip" Motor
The piezo inertia motor consists of three main parts: a flexure-coupled piezo actuator, a friction element, and a slider (the moving platform). During the "stick" part of a cycle, the piezo slowly expands under the ramp voltage, pushing the friction element and the slider forward in unison. During the "slip" part, the drive voltage drops rapidly and the piezo element returns to its starting length, with the friction element "slipping" backward. The slider does not move due to its inertia and the low coefficient of kinetic friction between the friction element and the bottom surface of the slider. The graph to the right shows the piezo drive voltage during one "stick-slip" cycle.
Repeating this cycle produces continuous forward travel of the slider. For travel in the reverse direction, the opposite drive voltage pattern is required, resulting in rapid piezo expansion and slower piezo contraction, or "slip-stick". During operation, the stage makes a high pitch noise and may generate some heat. This is normal behavior in the performance of the device and does not indicate a fault condition.
Due to a number of factors that include the application conditions, piezo hysteresis, component variance, and the axial load, the achieved step size will vary and is not repeatable. To help overcome this variance, an external feedback system will be necessary.
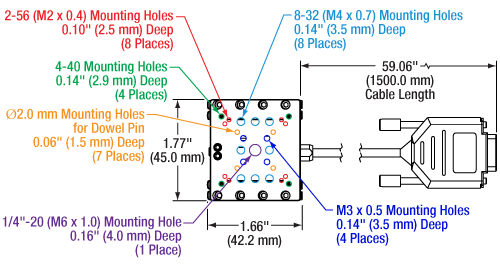
Click for Details
Mounting Features for the PDXZ1(/M) top plate. Dimensions for the metric stage are given in parentheses.
PDXZ1(/M) Stage Specifications | |
---|---|
Driving Controller | PDXC or PDXC2 Benchtop Controller |
Stage Type | Vertical Translation stage with Open- and Closed-Loop Piezo Inertia Drive |
Travel | 4.5 mm (0.18") |
Minimum Incremental Motiona | 100 nm |
Step Size Adjustabilityb | Minimum: 0.00001 mm Maximum: 2.25 mm |
Settling Time (Typical) | 400 ms |
Maximum Step Frequency | 20 kHz |
Speed (Typical, Continuous Stepping)a |
1 mm/s |
Average Speed Variation Over Travel Rangea |
±2% |
Optical Encoder Resolution | 12.5 nm |
Bidirectional Repeatability | ±0.75 µm |
Absolute Accuracy | ±2.5 µm |
Vertical Load Capacityc | 1 kg (2.2 lbs) |
Clamping / Holding Force | 20 N |
Pitch / Roll Over Travel Range | 200 µrad |
Lifetimed | ≥1.25 km |
Piezo Specifications | |
Max Operating Voltage | 60 V |
Piezo Capacitance | 170 nF |
Physical Specifications | |
Operating Temperature | 10 to 40 °C |
Cable Lengthe | 1.5 m (59") Cable Included |
Connector Type | 15-Pin D-SUB Female |
Dimensions (L x W x H) | 45.0 mm x 42.2 mm x 28.0 mm (1.77" x 1.66" x 1.10") |
End Range Dimensions (L x W) | 45.0 mm x 58.5 mm (1.77" x 2.30") |
Weight (Including Cable) | 310 g (10.94 oz) |
Products Compatible with PDXZ1(/M) Mounting Holes | |
---|---|
Hole Definition | Compatible Product Item # |
4-40, 2.9 mm (0.16") Deep | PDR1(/M), PDR1V(/M), ER-Series Cage Rods |
2-56 (M2 x 0.4), 0.10" (2.5 mm) Deep | PD1(/M), PD1D(/M), PDX1(/M), PDR1C(/M), PD1V(/M), PD1T(/M), PD1U(/M), PD1Z(/M) |
8-32 (M4 x 0.7), 0.14" (3.5 mm) Deep | PD1(/M), PD1V(/M), PDX1(/M), PD1B(/M) |
M3 x 0.5, 0.14" (3.5 mm) Deep | MMP1(/M), AMA011(/M), RB13P1(/M) |
1/4"-20 (M6 x 1.0) 0.16" (4.0 mm) Deep | - |
Ø2 mm Dowel Pin Holes, 1.5 mm (0.06") Deep | PD1(/M), PDX1(/M), PD1D(/M), PD1V(/M), PD1P1 |
PDXZ1(/M) Stage
Female 15-Pin D-Sub
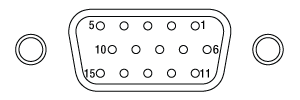
15-Pin D-Sub Pin Assignments
Pin(s) | Voltage Range | Name | Description |
---|---|---|---|
1 | -7.5 to +12.5 V | Encoder_B_N | Encoder B- |
2 | -7.5 to +12.5 V | Encoder_B_P | Encoder B+ |
3 | 0 V | GND | Digital Ground |
4 | -7.5 to +12.5 V | Encoder_A_N | Encoder A- |
5 | -7.5 to +12.5 V | Encoder_A_P | Encoder A+ |
6 | - | - | Reserved |
7 | - | - | Reserved |
8 | +5 V | +5 V | 5 V Power |
9 | -7.5 to +12.5 V | Encoder_Z_N | Encoder Z- |
10 | -7.5 to +12.5 V | Encoder_Z_P | Encoder Z+ |
11 | - | - | Reserved |
12 | 0 V | PGND | Power Ground |
13 | -10 to +50 V | SigOut1 | Piezo Output |
14 | 5 V TTL | EEPROM | 1-Wire EEPROM |
15 | - | - | Reserved |
Software
PDXC Version 2.1.0
The PDXC Software Package, which includes a GUI, drivers, and LabVIEW™/C++/Python SDK for third-party development.
Thorlabs offers the PDXC software package to interface with the PDXC Piezo Stage Controller. This controller is designed to drive the following piezo inertia stages:
- PDXZ1(/M) 4.5 mm Vertical Stage with Optical Encoder
- PD2(/M) 5 mm Linear Stage
- PDX2(/M) 5 mm Linear Stage with Optical Encoder
- PD1(/M) 20 mm Linear Stage
- PD1V(/M) Vacuum-Compatible 20 mm Linear Stage
- PD1D(/M) 20 mm Monolithic XY Stage
- PDX1(/M) 20 mm Linear Stage with Optical Encoder
- PDX1A(/M) 20 mm Low-Profile, Linear Stage with Optical Encoder
- PDX1AV(/M) Vacuum-Compatible 20 mm Low-Profile, Linear Stage with Optical Encoder
- PD3(/M) 50 mm Linear Stage
- PDR1C(/M) Rotation Stage
- PDXR1(/M) Rotation Stage with Optical Encoder
The software package allows two methods of usage: graphical user interface (GUI) utilities for direct interaction with and control of the controllers 'out of the box', and a set of programming interfaces for third-party development of custom-integrated positioning and alignment solutions to be easily programmed in the development language of choice (LabVIEW™/C++/Python SDK).
Software
Kinesis Version 1.14.50
The Kinesis Software Package, which includes a GUI for control of Thorlabs' Kinesis system controllers.
Also Available:
- Communications Protocol
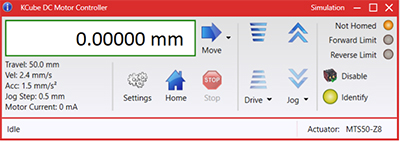
Kinesis GUI Screen
Thorlabs offers the Kinesis® software package to drive our wide range of motion controllers. The software can be used to control devices in the Kinesis family, which covers a wide variety of motion controllers ranging from small, low-powered, single-channel drivers (such as the K-Cubes™) to high-power, multi-channel benchtop units and modular 19" rack nanopositioning systems (the MMR60x Rack System).
The Kinesis Software features .NET controls which can be used by 3rd party developers working in the latest C#, Visual Basic, LabVIEW™, or any .NET compatible languages to create custom applications. Low-level DLL libraries are included for applications not expected to use the .NET framework and APIs are included with each install. A Central Sequence Manager supports integration and synchronization of all Thorlabs motion control hardware.
By providing this common software platform, Thorlabs has ensured that users can mix and match any of our motion control devices in a single application, while only having to learn a single set of software tools. In this way, it is perfectly feasible to combine any of the controllers from single-axis to multi-axis systems and control all from a single, PC-based unified software interface.
The software package allows two methods of usage: graphical user interface (GUI) utilities for direct interaction with and control of the controllers 'out of the box', and a set of programming interfaces that allow custom-integrated positioning and alignment solutions to be easily programmed in the development language of choice.
Legacy Software
Select products are still capable of running the legacy APT™ software package. Information on software compatibility can be found in the product documentation (), and additional details about the APT software can be found here.
Thorlabs' Kinesis® software features new .NET controls which can be used by third-party developers working in the latest C#, Visual Basic, LabVIEW™, or any .NET compatible languages to create custom applications.
C#
This programming language is designed to allow multiple programming paradigms, or languages, to be used, thus allowing for complex problems to be solved in an easy or efficient manner. It encompasses typing, imperative, declarative, functional, generic, object-oriented, and component-oriented programming. By providing functionality with this common software platform, Thorlabs has ensured that users can easily mix and match any of the Kinesis controllers in a single application, while only having to learn a single set of software tools. In this way, it is perfectly feasible to combine any of the controllers from the low-powered, single-axis to the high-powered, multi-axis systems and control all from a single, PC-based unified software interface.
The Kinesis System Software allows two methods of usage: graphical user interface (GUI) utilities for direct interaction and control of the controllers 'out of the box', and a set of programming interfaces that allow custom-integrated positioning and alignment solutions to be easily programmed in the development language of choice.
For a collection of example projects that can be compiled and run to demonstrate the different ways in which developers can build on the Kinesis motion control libraries, click on the links below. Please note that a separate integrated development environment (IDE) (e.g., Microsoft Visual Studio) will be required to execute the Quick Start examples. The C# example projects can be executed using the included .NET controls in the Kinesis software package (see the Kinesis Software tab for details).
![]() |
Click Here for the Kinesis with C# Quick Start Guide Click Here for C# Example Projects Click Here for Quick Start Device Control Examples |
![]() |
LabVIEW
LabVIEW can be used to communicate with any Kinesis- or APT-based controller via .NET controls. In LabVIEW, you build a user interface, known as a front panel, with a set of tools and objects and then add code using graphical representations of functions to control the front panel objects. The LabVIEW tutorial, provided below, provides some information on using the .NET controls to create control GUIs for Kinesis- and APT-driven devices within LabVIEW. It includes an overview with basic information about using controllers in LabVIEW and explains the setup procedure that needs to be completed before using a LabVIEW GUI to operate a device.
![]() |
Click Here to View the LabVIEW Guide Click Here to View the Kinesis with LabVIEW Overview Page |
![]() |
Achieving the Specified Performance
In this application note, we will discuss how to achieve the specified velocity and step size for the open-loop PD1(/M), PD1D(/M), and PDR1(/M) ORIC® Stages when driving them with KIM001 or KIM101 K-Cube™ Controllers; examples using the Kinesis® software and the K-Cube's front panel controls are discussed below. There are limitations when using an open-loop system, and we have created this application note to help minimize velocity and step size variation. We recommend using this application note upon initial setup, and/or if you are having issues with velocity and step size variation. For further details on how to change settings, please refer to the manuals of the individual stage and controller.
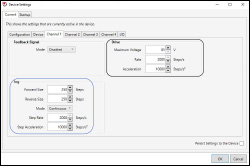
Click to Enlarge
Figure 2: These are the recommended channel settings for the PD(R) stage type. They can be changed in Device Settings -> Current Device Settings-> Channel 1.
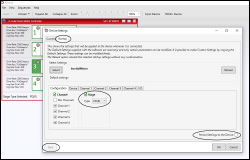
Click to Enlarge
Figure 1: When controlling an ORIC Stage, the stage type needs to be set to PD(R). This can be found in the Kinesis Software Device Settings -> Startup.
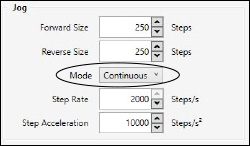
Click to Enlarge
Figure 4: Depicted in the circle is the jog mode, which should be set to continuous. This can be changed in Device Settings -> Current ->
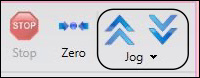
Figure 3: Circled in black are the jog buttons which can be found in the device GUI.
Kinesis© Software Control with a K-Cube Controller
The Kinesis software defaults the stage type to PIA, which is not applicable to ORIC stages; to change this, we need to change the startup settings. The startup settings can be found by first accessing the device settings in the device GUI panel and then clicking the Startup tab. Under the Configuration tab, change the stage type to PD(R), check the "Persist Settings to the Device" box on the bottom right, and click the "Save" button in the lower left corner. These selections are shown circled in Figure 1. By using these settings, the Kinesis software will use the PD(R) stage type. The other device and channel settings can also be changed in the startup settings.
With the PD(R) stage type, we recommend certain channel settings to achieve the specified speed, speed variation, and force. These settings can be changed in the "Channel 1" tab of the device settings and are depicted in Figure 2. We will be focusing on the settings in the “Drive” box, circled in black, and the "Jog" box, circled in blue.
For the "Drive" box, we recommend setting the "Maximum Voltage" to 85 V, the "Rate" at 2000 steps/s, and "Acceleration" to 10000 Steps/s2. For the settings in the "Jog" box, we recommend setting the "Forward Size" to 250 Steps, the "Reverse Size" to 250 Steps, the "Mode" to "Continuous", the "Step Rate" to 2000 Steps/s, and the "Step Acceleration" to 10000 Steps/s2. To achieve the specified results, it is important to make sure the stage is mounted properly to an even surface, to our recommended mounting plate, or to a compatible adapter plate.
A continuous jog at a step rate higher than 1000 steps/s can only be achieved by using the jog buttons in the device GUI, shown circled in Figure 3. Continuous jog movement is limited to within 1000 step/s when using the joystick on the KIM101 K-Cube Controller or wheel on the KIM001 K-Cube Controller. Single movement or movement by counts is not limited to 1000 step/s when using the joystick or wheel.
Please note that if you change the jog mode in Kinesis to "Continuous" or "Single" this will only influence the jog buttons in the Kinesis GUI, shown circled in Figure 3. This will not change the joystick mode on the KIM001 or KIM101 controller front panel. The jog mode can be found in Kinesis under Device settings -> Channel 1 -> "Jog" box -> "Mode", also shown in Figure 4. More information on this can be found in the Front Panel Control section, located below.
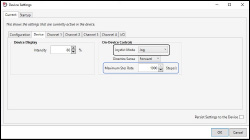
Click to Enlarge
Figure 6: Kinesis software showing the "Device" tab under Device Settings in the Device GUI. The "Maximum Step Rate" setting is circled in blue. To use the joystick with continuous jogging mode this setting must be less than 1000 steps/s. The Kinesis joystick modes can be selected via the dropdown menu circled in black.
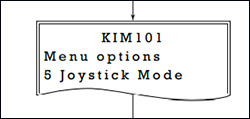
Figure 5: Drawing of the front panel of the KIM101 K-Cube Controller showing option 5, Joystick Mode.
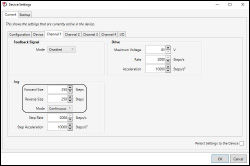
Click to Enlarge
Figure 8: Kinesis software showing where the step size can be changed using the "Forward Size" and "Reverse Size" settings. The "Mode" setting, also shown, only affects the controls of the jog buttons in the GUI and does not affect the joystick mode.
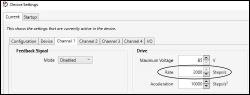
Click to Enlarge
Figure 7: The drive rate can be changed in the Kinesis software under Device Settings -> Current -> Channel 1. This is equivalent to Front Panel Control option 3, "Set Velocity".
KIMx01 Front Panel Control and Related Settings in Kinesis
There are 10 options on the front panel control menu. These can be accessed using the two buttons and joystick on the KIM101 K-Cube Controller or the button and wheel on the KIM001 K-Cube Controller.
Option 5, Joystick Mode, shown in Figure 5, has 3 modes: "Jog to Count", "Jogging in Steps", and "Velocity Control". The Joystick mode in the Kinesis software is related to option 5, Joystick Mode, on the front panel. The three options for the Joystick Mode in the Kinesis software are "Step Rate", "Jog", and "Goto Position". This setting is circled in black in Figure 6.
"Jog to Count" mode will move the stage to the target count, which is defaulted at 0, under the velocity that is set by option 3, "Set Velocity" on the front panel. The setting for option 3 is the velocity at which the stage will move for option 5’s “Jog to Count” mode and for option 1, "Goto Pos Count". There is an equivalent setting in Kinesis which can be found in Device Settings -> Channel 1 -> "Drive" box -> "Rate". This is shown in Figure 7.
In "Jogging in Steps" mode, option 3, "Set Velocity" does not change the stage's velocity. The velocity in this mode must be changed in the Kinesis software. This can be changed in Device settings -> Channel 1 -> "Jog" box -> "Step Rate". Instead of changing the step rate to increase the stage speed, the step size can be changed to increase the stage speed. The step size can be changed on the front panel of a KIM001 or KIM101 device through option 4, "Jog Step Size". This can also be achieved in Kinesis through Device settings -> "Channel 1" -> "Jog" box-> "Forward Size" and "Reverse Size", shown in Figure 8.
In option 5 "Velocity Control" mode, the joystick can be used to achieve continuous jogging, but only if the velocity is less than 1000 step/s. This velocity cannot be changed by option 3 on the front panel. The velocity can only be changed in the Kinesis software under the Device settings -> Device -> "Maximum Step Rate", shown in Figure 6. A value of 10000 may appear initially, but this value is not accepted by the software and must be revised to a number between 1 and 1000.
In Kinesis, the joystick mode "Step Rate", is related to the "Velocity Control" mode on the front panel and can use the setting of "Maximum Step Rate". The "Direction Sense" can be used to switch the travel direction when using the joystick or wheel.
Posted Comments: | |
No Comments Posted |
Motorized Linear Translation Stages
Thorlabs' motorized linear translation stages are offered in a range of maximum travel distances, from a stage with 20 µm of piezo translation to our 600 mm direct drive stage. Many of these stages can be assembled in multi-axis configurations, providing XY or XYZ translation. For fiber coupling applications, please see our multi-axis stages, which offer finer adjustment than our standard motorized translation stages. In addition to motorized linear translation stages, we offer motorized rotation stages and goniometers. We also offer manual translation stages.
Piezo Stages
These stages incorporate piezoelectric elements in a variety of drive mechanisms. ORIC® stages incorporate piezo inertia drives that use "stick-slip" friction properties to obtain extended travel ranges. Our Nanoflex™ translation stages use standard piezo chips along with manual actuators. Elliptec® stages use resonant piezo motors to push and pull the moving platform through resonant elliptical motion. Our LPS710E z-axis stage features a mechanically amplified piezo design and includes a matched controller.
Piezoelectric Stages | ||||
---|---|---|---|---|
Product Family | ORIC® PDXZ1 Closed-Loop 4.5 mm Vertical Stage |
ORIC® PD2 Open-Loop 5 mm Stage |
ORIC® PDX2 Closed-Loop 5 mm Stage |
|
Click Photo to Enlarge |
![]() |
![]() |
![]() |
|
Travel | 4.5 mm | 5 mm | ||
Speed | 1 mm/s (Typ.)a | 10 mm/s (Typ. Max)b | 8 mm/s (Typ.)c | |
Drive Type | Piezoelectric Inertia Drive | |||
Possible Axis Configurations | Z | X, XY, XYZ | ||
Mounting Surface Size |
45.0 mm x 42.0 mm | 13 mm x 13 mm | ||
Additional Details |
Piezoelectric Stages | ||||||
---|---|---|---|---|---|---|
Product Family | ORIC® PD1 Open-Loop 20 mm Stage |
ORIC® PD1D Open-Loop 20 mm Monolithic XY Stage |
ORIC® PDX1 Closed-Loop 20 mm Stage |
ORIC® PDX1A Closed-Loop 20 mm Stage Low-Profile |
ORIC® PD3 Open-Loop 50 mm Stage |
|
Click Photo to Enlarge |
![]() |
![]() |
![]() |
![]() |
![]() |
|
Travel | 20 mm | 50 mm | ||||
Speed | 3 mm/s (Typ. Max)a | 20 mm/s (Typ. Max)c | 10 mm/s (Typ.)b | 10 mm/sd | ||
Drive Type | Piezoelectric Inertia Drive | |||||
Possible Axis Configurations | X, XY, XYZ | XY, XYZ | X, XY, XYZ | X, XY, XYZ | X, XY, XYZ | |
Mounting Surface Size |
30 mm x 30 mm | 80 mm x 30 mm | ||||
Additional Details |
Piezoelectric Stages | ||||||
---|---|---|---|---|---|---|
Product Family | Nanoflex™ 20 µm Stage with 5 mm Actuator |
Nanoflex™ 25 µm Stage with 1.5 mm Actuator |
Elliptec® 28 mm Stage | Elliptec® 60 mm Stage | LPS710E 1.1 mm Vertical Stage | |
Click Photo to Enlarge |
![]() |
![]() |
![]() |
![]() |
![]() |
|
Travel | 20 µm + 5 mm Manual | 25 µm + 1.5 mm Manual | 28 mm | 60.0 mm | 1.1 mm | |
Maximum Velocity | - | 180 mm/s | 90 mm/s | - | ||
Drive Type | Piezo with Manual Actuator | Resonant Piezoelectric Motor | Amplified Piezo | |||
Possible Axis Configurations | X, XY, XYZ | X | Z | |||
Mounting Surface Size | 75 mm x 75 mm | 30 mm x 30 mm | 15 mm x 15 mm | 21 mm x 21 mm | ||
Additional Details |
Stepper Motor Stages
These translation stages feature removable or integrated stepper motors and long travel ranges up to 300 mm. Many of these stages either have integrated multi-axis capability (PLSXY) or can be assembled into multi-axis configurations (PLSX, LNR Series, NRT Series, and LTS Series stages). The MLJ150 stage also offers high load capacity vertical translation.
Stepper Motor Stages | |||||
---|---|---|---|---|---|
Product Family | PLSX with and without PLST(/M) Top Plate 1" Stage |
PLSXY with and without PLST(/M) Top Plate 1" Stage |
LNR Series 25 mm Stage |
LNR Series 50 mm Stage |
|
Click Photo to Enlarge |
![]() |
![]() |
![]() |
![]() |
|
Travel | 1" | 25 mm | 50 mm | ||
Maximum Velocity | 7.0 mm/s | 2.0 mm/s | 50 mm/s | ||
Possible Axis Configurations |
X, XY | X, XY, XYZ | X, XY, XYZ | ||
Mounting Surface Size |
3" x 3" | 60 mm x 60 mm | 100 mm x 100 mm | ||
Additional Details |
Stepper Motor Stages | ||||||
---|---|---|---|---|---|---|
Product Family | NRT Series 100 mm Stage |
NRT Series 150 mm Stage |
LTS Series 150 mm Stage |
LTS Series 300 mm Stage |
MLJ250 50 mm Vertical Stage |
|
Click Photo to Enlarge |
![]() |
![]() |
![]() |
![]() |
![]() |
|
Travel | 100 mm | 150 mm | 150 mm | 300 mm | 50 mm | |
Maximum Velocity | 30 mm/s | 50 mm/s | 3.0 mm/s | |||
Possible Axis Configurations |
X, XY, XYZ | X, XY, XYZ | Z | |||
Mounting Surface Size |
84 mm x 84 mm | 100 mm x 90 mm | 148 mm x 131 mm | |||
Additional Details |
DC Servo Motor Stages
Thorlabs offers linear translation stages with removable or integrated DC servo motors. These stages feature low profiles and many can be assembled in multi-axis configurations.
DC Servo Motor Stages | ||||
---|---|---|---|---|
Product Family | MT Series 12 mm Stages |
PT Series 25 mm Stages |
MTS Series 25 mm Stage |
MTS Series 50 mm Stage |
Click Photo to Enlarge |
![]() |
![]() |
![]() |
![]() |
Travel | 12 mm | 25 mm | 25 mm | 50 mm |
Maximum Velocity | 2.6 mm/s | 2.4 mm/s | ||
Possible Axis Configurations | X, XY, XYZ | X, XY, XYZ | ||
Mounting Surface Size |
61 mm x 61 mm | 101.6 mm x 76.2 mm | 43 mm x 43 mm | |
Additional Details |
DC Servo Motor Stages | ||||
---|---|---|---|---|
Product Family | M30 Series 30 mm Stage |
M30 Series 30 mm Monolithic XY Stage |
M150 Series 150 mm XY Stage |
KVS30 30 mm Vertical Stage |
Click Photo to Enlarge |
![]() |
![]() |
![]() |
![]() |
Travel | 30 mm | 150 mm | 30 mm | |
Maximum Velocity | 2.4 mm/s | X-Axis: 170 mm/s Y-Axis: 230 mm/s |
8.0 mm/s | |
Possible Axis Configurations | X, Z | XY, XZ | XY | Z |
Mounting Surface Size |
115 mm x 115 mm | 272.4 mm x 272.4 mm | 116.2 mm x 116.2 mm | |
Additional Details |
Direct Drive Stages
These low-profile stages feature integrated brushless DC servo motors for high speed translation with zero backlash. When no power is applied, the platforms of these stages have very little inertia and are virtually free running. Hence these stages may not be suitable for applications where the stage's platform needs to remain in a set position when the power is off. We do not recommend mounting these stages vertically.
Direct Drive Stages | |||||
---|---|---|---|---|---|
Product Family | DDS Series 50 mm Stage |
DDS Series 100 mm Stage |
DDS Series 220 mm Stage |
DDS Series 300 mm Stage |
DDS Series 600 mm Stage |
Click Photo to Enlarge |
![]() |
![]() |
![]() |
![]() |
![]() |
Travel | 50 mm | 100 mm | 220 mm | 300 mm | 600 mm |
Maximum Velocity | 500 mm/s | 300 mm/s | 400 mm/s | 400 mm/s | |
Possible Axis Configurations | X, XY | X, XY | X | X | |
Mounting Surface Size | 60 mm x 52 mm | 88 mm x 88 mm | 120 mm x 120 mm | ||
Additional Details |

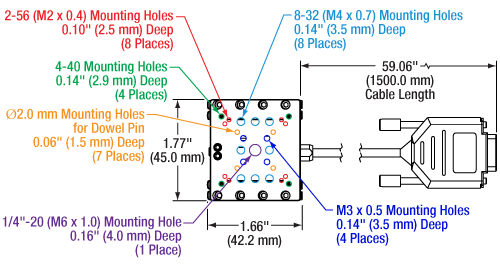
Click for Details
Mounting Features for the PDXZ1(/M) top plate. Dimensions for the metric stage are given in parentheses, while callouts without an imperial and metric dimension are the same for both stages.
- Open- and Closed-Loop Operation Supported
- Optical Encoder Provides 12.5 nm Resolution
- Typical, Continuous Stepping Moving Speed of 1 mm/s
- Integrated 1.5 m (59") Cable with 15-Pin D-Sub Female Connector
- Requires the PDXC or PDXC2 Piezo Inertia Controller (Sold Separately Below)
This ORIC vertical travel piezo inertia stage with integrated optical encoder is able to operate in both open- and closed-loop modes, can support vertical loads up to 1 kg, and operates with an accuracy of ±2.5 µm. The piezo inertia drive is self-locking when the stage is at rest and no power is supplied to the piezo, making these actuators ideal for set-and-hold applications that require micrometer resolution and long-term alignment stability. See the Specs tab for detailed specifications.
After each stage is manufactured, the pitch and roll of the stage are tested. This ensures that each stage meets the stated specifications over the full translation range of the stage. A summary of the test results is provided on a data sheet that ships with each stage. A sample data sheet can be viewed here.
The stage should be placed on a surface with flatness ≤5 µm. The PD1B3(/M) mounting adapter (sold below) provides a mounting surface with precise flatness to avoid warping the stage when mounting it to a table or breadboard surface. Alternative top plate adapters are available below.
Each stage has an integrated 1.5 m cable with a 15-pin D-sub connector that can connect directly to a PDXC or PDXC2 controller. If additional cable length is needed, the 3 m long PDXCE Extension Cable (available separately below) can be used. Due to the capacitance of the cables, do not use cables longer than 4.5 m in total when connecting the stage to a PDXC or PDXC2 controller.

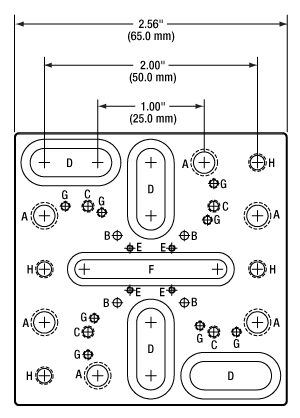
Click for Details
Mechanical Drawing for the PD1B3(/M) Adapter Plate. See the table on the left for descriptions of the hole labels. Dimensions for the metric version of the adapter plate are given in parentheses.
- Provide Flat Surface for Mounting ORIC Stages
- Passivated Stainless Steel Construction
- Reduces Stage Warping When Mounting to Table or Breadboard
- Dimensions (L x W x H): 65.0 mm x 65.0 mm x 10.0 mm
Thorlabs' PD1B3(/M) Universal Adapter Plate provides a flat surface (flatness ≤5 µm) for mounting ORIC piezo inertia stages. Mounting holes are labeled in the mechanical drawing to the right corresponding to the table below. The four 4-40 threaded holes are 30 mm cage system compatible, and two 1/4"-20 (M6) screws are included for mounting to breadboards.
If the stage is mounted on a surface with >5 µm flatness (as with most breadboards and optical tables), the velocity variation and pitch/yaw of the stage may suffer due to the stage warping. Mounting the stage on the adapter drastically reduces the amount the stage warps when mounted on a table or breadboard with insufficient flatness.
Labela | Holes/Slots Patternb | Spacingb (Stage Compatibility) | Threading Depth | Places |
---|---|---|---|---|
A | 1/4"-20 (M6) | 1" x 2" (25 x 50 mm) | Through | 6 |
B | Ø2 mm Dowel Pin Holes |
16 x 16 mm | 1.5 mm | 4 |
C | 4-40 | 30 x 30 mm (Item #s PDR1(/M), PDR1V(/M)) | 3.5 mm | 4 |
D | 1/4" (M6) Counterbored Slot | 1" to 2" (25 to 50 mm) | N/A | 4 |
E | 00-90 (M1.2) | 10 x 10 mm (Item #s PD2(/M), PDX2(/M)) | 3 mm | 4 |
F | #8 (M4) Counterbored Slot | 1.25" (31.25 mm) | N/A | 1 |
G | 2-56 (M2) | 27.0 x 23.4 mm (Item #s PDXZ1(/M), PD1(/M), PD1V(/M), PDX1(/M), PDX1A(/M), PDX1AV(/M), PD1D(/M), PDR1C(/M)) / 40.8 x 30 mm |
7 mm | 8 |
H | 8-32 (M4) | 2" (50 mm) (Item # PD3(/M)) / 2" x 2" (50 x 50 mm) (Item # PDXR1(/M)) | 7.8 mm | 4 |

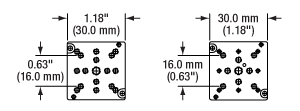
Click for Details
PD1T and PD1T/M Adapter Plate Schematics
The image on the left shows the PD1U(/M) adapter plate schematics while the image on the right shows the PD1B(/M) mounting adapter schematic.
- Provide Different Mounting Hole Patterns and Capabilities
- Mounting To PDXZ1(/M) Stage:
- PD1T(/M) and PD1U(/M): Two #2 (M2) Counterbored Holes
- PD1B(/M): #8 (M4) Counterbored Slot
- Included Mounting Components
- PD1T(/M) and PD1U(/M): Two 2-56 (M2) Screws and Two Ø2 mm Dowel Pins
- PD1B(/M): Two 8-32 (M4) Screws and Two #8 (M4) Washers
These adapter plates can be mounted directly to the top plate of the PDXZ1(/M) vertical stage to provide alternate mounting capabilities. Each plate has a 30 mm x 30 mm footprint which matches our 20 mm travel piezo inertia stages.
The PD1T imperial adapter plate features a central 8-32 tapped hole and sixteen 4-40 tapped holes, four of which are spaced for 16 mm cage systems. The metric version features a central M4 tapped hole, ten M2 mounting taps, four M3 mounting taps, and four 4-40 taps with 16 mm cage system spacing.
The PD1U imperial adapter plate features four 6-32 and four 8-32 tapped holes in a cross pattern; the metric version features eight M4 tapped holes in the same layout. The bottom surface features five #8 (M4) counterbores, as well as four Ø2 mm dowel pin holes for alignment. See the drawing above for more details.
The PD1B(/M) adapter features a #8 (M4) mounting slot that can be used to mount the adapter to the top surface of the PDXZ1(/M) stage. A 20 mm travel piezo inertia stage or other component can then be mounted to the adapter using the 2-56 (M2) tapped mounting holes.

Key Specificationsa | ||
---|---|---|
SMC Port | Number of Ports | Two |
Voltage | 0 to 40 V | |
Frequency | 20 kHz Max | |
D-Sub Port | Number of Ports | One |
Voltage | -10 to 50 V | |
Frequency | 20 kHz Max | |
Max Current Limit | 10 A | |
Front USB | Type A, USB Host 2.0 | |
Back USB | Type B, USB Device 2.0 | |
Voltage of Analog In/Out | -10 to 10 V, ±2% | |
Voltage of Trigger In/Out | 0 to 5 V, TTL | |
Input Power | 100 - 240 VAC, 50 - 60 Hz |
- Controller for ORIC Piezo Inertia Linear Stages, PDXZ1(/M) Vertical Stage, and both PDR1C(/M) and PDXR1(/M) Rotation Stages
- Supports Both Open- and Closed-Loop Operation
- SMC and 15-Pin D-Sub Ports Available
This controller is designed to control our ORIC piezo-inertia-driven linear stages, PDXZ1(/M) vertical stage, and both PDR1C(/M) and PDXR1(/M) rotation stages. It offers two channels that support open-loop stage control using SMC outputs and one channel that can provide open- or closed-loop stage control using a 15-pin D-sub output. If a longer connection is required for ORIC stages with a D-Sub connector, the PDXCE Extension Cable can be used (sold separately below).
Embedded software allows this unit to be fully controlled using the buttons, LCD display, and knob on the front panel. Alternatively, built-in external trigger modes support single-channel operation. By connecting multiple controllers together, multi-channel operation in D-sub mode such as a raster scan is possible. Users can select the output port(s), switch between open-loop and closed-loop modes, and perform homing and encoder calibration without being connected to a PC. In addition to these on-unit controls, USB connectivity provides simple PC-control with our available software platform.
The unit comes with a compatible region-specific power cord. For all applications, use an IEC320 compatible power cord fitted with a plug appropriate for your particular power socket. Ensure the line voltage rating marked on the rear panel agrees with your local power supply.
For more information, please see our full web presentation.

Key Specificationsa | ||
---|---|---|
Performance Specificationsa | ||
D-sub Port | Number of Ports | One |
Voltage | 0 to 56 V | |
Frequency | 20 kHz Max | |
Max Current Limit | 10 A | |
Front USB | Type A, USB HID Host | |
Back USB | Type B, USB Device 2.0 | |
I/O Port | Voltage of Analog In/Out | -10 to 10 V, ±2% |
Voltage of Trigger In/Out | 0 to 5 V, TTL | |
Ethernet PC Communication | One RJ-45 Port | |
Dimensions (L x W x H) | 115.2 mm x 150.0 mm x 48.5 mm (4.54” x 5.91” x 1.91”) |
|
Weight | 0.53 kg | |
Input Power | 12 V, 3 A DAC |
- Controller for ORIC Piezo Inertia Linear Stages, PDXZ1(/M) Vertical Stage, and both PDR1C(/M) and PDXR1(/M) Rotation Stages
- Compact Design and PC Control with Kinesis® Software
- Supports Both Open- and Closed-Loop Operation
- Energy Efficient Switch Amplifier Circuit Outputs Peak Current of 10 A
- Configurable High Speed Communication Interfaces: USB 2.0, Gigabit Ethernet, Digital I/0, Analog I/0
- 800 Hz to 20 kHz Pulse Rate Range
The PDXC2 compact controller is designed for our ORIC piezo-inertia-driven linear stages, PDXZ1(/M) vertical stage, and both PDR1C(/M) and PDXR1(/M) rotation stages. It features one channel that supports open- or closed-loop stage control using a 15-pin D-sub output. The PDXC2AD D-sub to SMC adapter cable (sold below) can be used to operate stages with an SMC connection in open-loop mode.
The PDXC2 controller is connected to PC by either the USB or ethernet ports on the back panel of the controller. All the operating parameters and operations, such as switching between open- and closed-loop modes, performing homing operation, and parameter optimization are controlled by PC with the Kinesis® software (available for download on the Kinesis Software tab above). Settings such as trigger modes and movement parameters can be configured for operations such as raster scans. Calibration for specific ORIC stages with encoders (Item #s PDX1(/M), PDX1A(/M), PDX1AV(/M), and PDXR1(/M) only) is performed with the PDXC2 Calibration Tool found on the Motion Control Software page. Please see the user manual for details. Command-line control is also possible through the USB and RS-232 ports.
The PDXC2 unit is powered by the included DS12 12 VDC power adapter, which operates at an input voltage of 100 - 240 VAC and ships with a region-specific AC cable. For all applications, use an IEC320 compatible power cord fitted with a plug appropriate for your particular power socket. Make sure that the line voltage rating marked on the power adapter agrees with your local power supply.
For more information, please see our full web presentation.

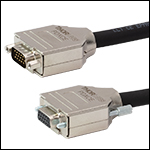
Click to Enlarge
DB15 Male to DB15 Female
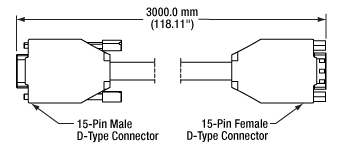
Click to Enlarge
Mechanical Drawing
- Connects Female D-Sub Connector on a PDXZ1(/M), PD2(/M), PDX2(/M), PDX1(/M), PDX1A(/M), PDX1AV(/M), PD3(/M) or PDXR1(/M) Stage to PDXC or PDXC2 Piezo Inertia Stage Controller
- 3000.0 mm (118.11") of Extra Length
The PDXCE extension cable provides 3000.0 mm (118.11") of extra cord length, if needed, when connecting ORIC stages with a Female D-Sub Connector to the PDXC or PDXC2 ORIC Inertia Stage Controllers. Due to the capacitance of the cables, each stage has a recommended maximum cable length. Please check individual stage specifications before adding extension cables.

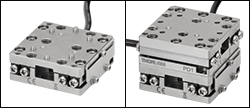
Click for Details
PD1P1 Dowel Pins fit into the mounting holes of most ORIC® Stages, as shown in the PD1 Stage above.
- Ø2 mm, 3 mm Long Dowel Pins
- Corrosion-Resistant Stainless Steel
- Sold in Packs of 20
The PD1P1 Dowel Pins are 2 mm in diameter and are 3 mm long. They serve as replacements for the dowel pins that are included with Thorlabs' 4.5 mm Vertical, 20 mm, 50 mm, Rotating, and Vacuum-Compatible ORIC® Stages. Composed of stainless steel, the dowel pins are corrosion-resistant.
The dowel pins are sold in packs of 20.